Beschriftungslaser
Beschriftungslaser
Laserbearbeitung
Batterie-Beschriftung mit Lasertechnologie
Laserbeschriftung und -bearbeitung spielen in der Fertigung von Batterien eine wichtige Rolle – sowohl in der Herstellung als auch im Qualitätsmanagement.
Die Batterie-Beschriftung mit dem UV-Laser MD-U bzw. dem Hybrid-Laser MD-X von KEYENCE bietet entscheidende Vorteile:
- Reduzierung des Wärmestresses & Sicherstellung der Rückverfolgbarkeit
- Beschädigungsfreie & dauerhafte Markierung
- Einhaltung der Qualitätsstandards unterschiedlicher Länder.
Batterie-Beschriftung: Vorteile und Batterietypen
Die Batterie-Beschriftung ist mittlerweile ein bedeutender Aspekt der Elektrofahrzeugindustrie. Elektrofahrzeuge (EV), Plug-in-Hybride (PHV) und Hybridfahrzeuge (HV) – betrieben durch Lithium-Ionen-Batterien – werden immer beliebter. Auch mobile Ladestationen sind mittlerweile allgegenwärtig.
Die Lithium-Ionen-Batterien in Elektro- und Hybridfahrzeugen weisen im Vergleich zu herkömmlichen Batterien eine größere Kapazität und eine kompaktere bzw. leichtere Bauweise auf, was besonders präzise Markierungen unverzichtbar macht.
Entdecken Sie mehr über dieses Produkt.
Klicken Sie hier, um Ihre Demo zu buchen.
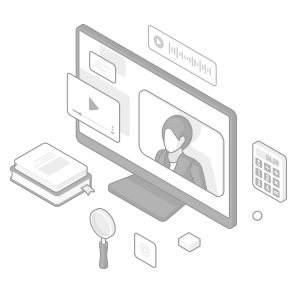
Vorteile der Beschriftung von Batterien mit Lasertechnologie
Eine dauerhafte, beschädigungsfreie und exakte Beschriftung, deren Informationen in Sekunden abgerufen werden können, spielt eine entscheidende Rolle für die Sicherheit, Rückverfolgbarkeit und Nachhaltigkeit von Batterien.
Die Lasertechnologie bietet hier die ideale Lösung, um den hohen Anforderungen moderner Batteriehersteller gerecht zu werden. Die Vorteile der Lasermarkierung auf einen Blick:
- Dauerhaftigkeit: Widersteht Hitze, Chemikalien und Abrieb.
- Präzision: Hochauflösende Markierungen, selbst auf kleinsten Flächen.
- Nachhaltigkeit: Keine Verbrauchsmaterialien wie Tinte oder Etiketten.
- Flexibilität: Anpassbar an verschiedene Materialien wie Kunststoff oder Metall.
- Fälschungssicherheit: Manipulationssicher, da sie sich nicht entfernen lässt, ohne das Produkt zu beschädigen.
- Effizienz: Schnelle Verarbeitung ohne Werkzeugwechsel.
- Konformität: Erfüllt internationale Normen wie ISO 9001 und andere branchenspezifische Anforderungen.
Kontaktieren Sie uns und erfahren Sie, wie unsere fortgeschrittene Technologie hilft, um Ihr Business aufs nächste Level zu heben.
Kontakt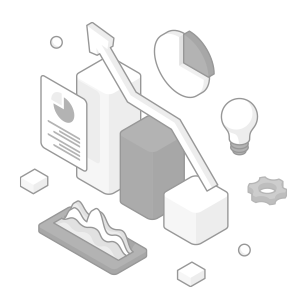
3 Batterietypen in Elektro- und Hybridfahrzeugen
In EV-, PHV- und HV-Fahrzeugen handelt es sich um zylindrische, prismatische und Pouch-Batterien.
Im Folgenden sehen Sie eine grafische Darstellung der 3 Typen sowie eine Tabelle mit den wichtigsten Eigenschaften im Vergleich.
Zylindrisch
Prismatisch
Pouch
Merkmal | Zylindrisch | Prismatisch | Pouch |
---|---|---|---|
Kapazität
|
Zylindrisch
2.300 - 26.000 mAh
(abhängig von der Größe) |
Primatisch
20.000 - 30.000 mAh
|
Pouch
2.300 - 26.000 mAh
(abhängig von der Größe) |
Lebensspanne
|
Zylindrisch
25.000 Ladezyklen
|
Primatisch
2.000 Ladezyklen
|
Pouch
2.000 Ladezyklen
|
Größe
|
Zylindrisch
Mittel
|
Primatisch
Groß
|
Pouch
Klein
|
Kosten
|
Zylindrisch
Niedrig
|
Primatisch
Mittel
|
Pouch
Hoch
|
Überhitzungsrisiko
|
Zylindrisch
Gering
|
Primatisch
Mittel
|
Pouch
Hoch
|
Erfunden
|
Zylindrisch
1880er
|
Primatisch
1960er
|
Pouch
1970er
|
Zellenspalten
|
Zylindrisch
Ja
|
Primatisch
Nein
|
Pouch
Nein
|
Gewicht
|
Zylindrisch
Schwer
|
Primatisch
Mittel
|
Pouch
Leicht
|
Chemische Zusammensetzung
|
Zylindrisch
Lithium-Ionen,
Aluminium- oder Stahlgehäuse |
Primatisch
Lithium-Ionen,
Aluminium- oder Stahlgehäuse |
Pouch
Lithium,
Polymer-beschichtete Aluminiumfolie |
Genutzt von
|
Zylindrisch
Tesla
|
Primatisch
BMW (Bayerische Motorwerke), Volkswagen
|
Pouch
GM (General Motors)
|
Kontaktieren Sie uns und erfahren Sie, wie unsere fortgeschrittene Technologie hilft, um Ihr Business aufs nächste Level zu heben.
Kontakt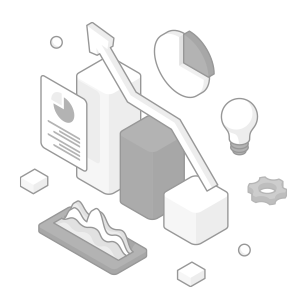
Batterie beschriften mit dem UV-Laser & Hybrid-Laser von KEYENCE
Faserlaser haben hohe Leistungen und verursachen typischerweise Wärmestress und Partikel während der Markierung. Das kann Produktionsprobleme verursachen. Der UV-Laser MD-U und der Hybrid-Laser MD-X von KEYENCE reduzieren den Wärmestress, um eine nahezu beschädigungsfreie Markierung von Lithiumbatterien – auch auf dünnen Elektroden – zu ermöglichen.
- Der MD-U reduziert die Wärme durch die Verwendung einer stark absorbierenden Wellenlänge (355 nm) und erreicht so eine "kalte Markierung".
- Der MD-X mindert durch hohe Spitzenleistung und kurze Pulsdauer Schäden bei der Batterieproduktion. So ist eine rasche Markierung möglich.
Die folgende Darstellung zeigt Ihnen die präzise, materialschonende Beschriftung von Batterien mit den Lasern von KEYENCE im Vergleich zum Faserlaser.
UV-Laser / Hybrid-Laser
Faserlaser
Entdecken Sie mehr über dieses Produkt.
Klicken Sie hier, um Ihre Demo zu buchen.
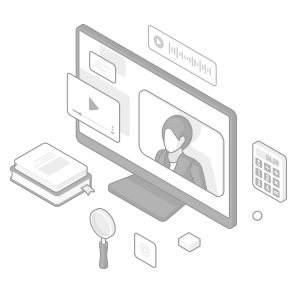
Beschriftung auf Kathoden- und Anodenfolien
Im ersten Schritt der Batterieproduktion erhalten Hersteller eine Slurry (halbflüssiges Metall). Nach der Aufnahme der aktiven Masse, wie etwa Lithium-Kobaltoxid, Lithium-Manganat-Oxid oder Lithium-Eisen-Phosphat, werden Kathoden- und Anodenfolien zunächst gepresst und anschließend zugeschnitten.
Laserbeschriftungssysteme markieren diese Batterie-Folien entsprechend den Prüfergebnissen, die beispielsweise Informationen zur Dicke oder zu möglichen Fehlern enthalten.
Dank hochpräziser Lasertechnologie lassen sich verschiedene Zeichen und Formen (als 2D-Codes, Seriennummern oder als Design) direkt auf der Folie aufbringen. Dies unterstützt eine exakte Rückverfolgbarkeit und die Qualitätssicherung im gesamten Produktionsprozess.
Die Laserbeschriftung, insbesondere von 2D-Codes, ist einfach zu realisieren. KEYENCEs vielfältige Laser bieten die ideale Lösung für jede Anwendung zur 2D-Code-Markierung. Dank führender Strahlsteuerung und integrierter 2D-Code-Leseoptionen sind die KEYENCE-Lasermodelle ideal für Ihre Anforderungen an Nachverfolgbarkeit.

- 2x
- 1.75x
- 1.5x
- 1.25x
- 1x, ausgewählt
- 0.75x
- 0.5x
- Kapitel
- Beschreibungen aus, ausgewählt
- Untertiteleinstellungen, öffnet Einstellungen für Untertitel
- Untertitel aus, ausgewählt
- en (Main), ausgewählt
This is a modal window.
Anfang des Dialogfensters. Esc bricht ab und schließt das Fenster.
Ende des Dialogfensters.
This is a modal window. Durch Drücken der Esc-Taste bzw. Betätigung der Schaltfläche "Schließen" wird dieses modale Fenster geschlossen.
2D-Code-Kennzeichnung von Batteriegehäusen
Die Kennzeichnung von Batteriekappen mit 2D-Codes, die detaillierte Herstellungsinformationen enthalten, verbessert das Rückverfolgbarkeitsmanagement erheblich.
2D-Codes können große Mengen an Informationen speichern, die in Sekunden abgerufen werden können. Zu den gespeicherten Daten zählen oft der Fertigungszeitpunkt, die einzelnen Schritte in der Lieferkette, die verwendeten Materialien und sogar der Name der beteiligten Fachkraft.
Ein durchdachtes Rückverfolgbarkeitsmanagement schützt sowohl Kunden als auch Hersteller vor Ausschuss:
- Hersteller können defekte Produkte schnell zurückrufen und die Ursache des Problems identifizieren. Gleichzeitig erhalten Kunden Zugriff auf umfassende Informationen zu ihrem Produkt.
- Durch die Möglichkeit, fehlerhafte Chargen frühzeitig zu stoppen, bevor sie weiter in den Verkauf gelangen, minimieren Hersteller Verluste und verbessern ihre Prozesskontrolle.
Da Vorschriften für EV-, PHV- und HV-Fahrzeuge weltweit variieren, werden oft mehrere 2D-Codes markiert. Diese gewährleisten, dass die Lithium-Ionen-Batterien den unterschiedlichen Qualitätsstandards der jeweiligen Länder entsprechen.

- 2x
- 1.75x
- 1.5x
- 1.25x
- 1x, ausgewählt
- 0.75x
- 0.5x
- Kapitel
- Beschreibungen aus, ausgewählt
- Untertiteleinstellungen, öffnet Einstellungen für Untertitel
- Untertitel aus, ausgewählt
- en (Main), ausgewählt
This is a modal window.
Anfang des Dialogfensters. Esc bricht ab und schließt das Fenster.
Ende des Dialogfensters.
This is a modal window. Durch Drücken der Esc-Taste bzw. Betätigung der Schaltfläche "Schließen" wird dieses modale Fenster geschlossen.
Wir informieren Sie gerne über weitere Details.
Noch heute melden!
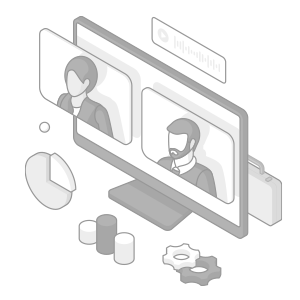
2D-Code-Markierung auf Versiegelungsband: flache Oberflächen & 3D-Formen
Die Beschriftung von Batterien erfordert höchste Präzision, um den Anforderungen der modernen Fertigung gerecht zu werden. Mit der Kombination aus 3-Achsen-Steuerung und Z-Tracking bietet die Modellreihe MD-X- innovative Lösungen für flexible und zuverlässige Beschriftungen.
3-Achsen-Steuerung
Die 3-Achsen-Steuerungen ermöglichen es den MD-X- und MD-U-Lasern, ihre Fokusdistanzen über einen Bereich von 42 mm (+/- 21 mm) anzupassen. Dadurch kann jeder Laser sowohl flache Oberflächen als auch 3D-Formen wie Zylinder, Prismen oder freie Formen präzise markieren und bietet so Flexibilität für die Hersteller von Lithiumbatterien.
Durch die 3-Achsen-Steuerung bleibt der Laserstrahl während des gesamten Markierungsprozesses im Fokus. So kann eine gleichmäßige Markierung auch über eine große Beschriftungsfläche hinweg durchgeführt werden. Es entsteht kein Kisseneffekt an den Rändern.
Die folgende Darstellung zeigt Ihnen den Unterschied zwischen der konventionellen Methode und der Beschriftung mit MD-X von KEYENCE. Bei der konventionellen Methode werden die Zeichen dicker und ihre Positionen verschieben sich, je näher sie am Rand des Bereichs liegen (Kisseneffekt). Der MD-X wiederum sorgt für eine gleichmäßige Linienbreite im gesamten Bereich.
Konventionelle Modelle
MD-X
Z-Tracking
Eine Neigung von Bauteilen während der Produktion und des Transports verändert die Fokusdistanz und erschwert die Markierung für Batteriezellenhersteller. Das MD-X-System löst dieses Problem mit Z-Tracking: Es misst den Abstand der zu beschriftenden Oberfläche, passt den Fokus automatisch an und dreht die Beschriftung so, dass sie genau an der vorgesehenen Stelle platziert wird.
Markierung auf einer flachen Oberfläche
Markierung auf einer zylindrischen Oberfläche
Interessiert an unseren Preisen?
Klicken Sie hier, um mehr zu erfahren.
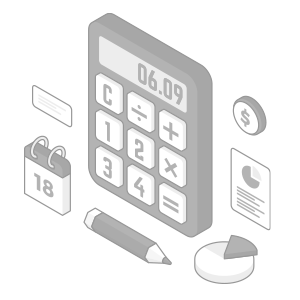
Weitere Einsatzbereiche der Laser von KEYENCE
In der Batterieherstellung sind nicht nur die Markierung und Beschriftung wichtig, sondern auch die Reinigung und das Aufrauen der Oberflächen.
Entfernung von Fremdstoffen auf Elektroden
Fremdstoffe und/oder Oxidschichten auf Elektroden bilden beim Schweißprozess Poren, die die Festigkeit der Schweißnaht beeinträchtigen. Laser verbessern die Schweißqualität durch das Reinigen der zu verbindenden Oberflächen.

- 2x
- 1.75x
- 1.5x
- 1.25x
- 1x, ausgewählt
- 0.75x
- 0.5x
- Kapitel
- Beschreibungen aus, ausgewählt
- Untertiteleinstellungen, öffnet Einstellungen für Untertitel
- Untertitel aus, ausgewählt
- en (Main), ausgewählt
- 1080p1080pHD
- 900p900pHD
- 720p720pHD
- 540p540p
- 360p360p
- 216p216p
- Autom.A, ausgewählt
This is a modal window.
Anfang des Dialogfensters. Esc bricht ab und schließt das Fenster.
Ende des Dialogfensters.
This is a modal window. Durch Drücken der Esc-Taste bzw. Betätigung der Schaltfläche "Schließen" wird dieses modale Fenster geschlossen.
Oberflächenaufrauung des Batteriedeckels
Im Batterieherstellungsprozess müssen die Haftoberflächen des Batteriedeckels und des Gehäuses aufgeraut werden, um die Haftfestigkeit zu verbessern. Laser werden für diesen Prozess eingesetzt, da sie die Oberfläche aufrauen können, ohne die innen gelegenen Bestandteile zu beschädigen.
Materialschonende & dauerhafte Batterie-Beschriftung mit KEYENCE
Die Batterieindustrie stellt hohe Anforderungen an Kompaktheit, Rückverfolgbarkeit und Qualitätskontrolle. Hersteller von Batteriezellen und Zulieferer profitieren daher von präzisen, langlebigen, kosteneffizienten und fälschungssicheren Lasermarkierungen. Kontaktieren Sie uns, um die perfekte KEYENCE-Lösung für Ihre Beschriftungsanforderungen zu finden.
Kontaktieren Sie uns und erfahren Sie, wie unsere fortgeschrittene Technologie hilft, um Ihr Business aufs nächste Level zu heben.
Kontakt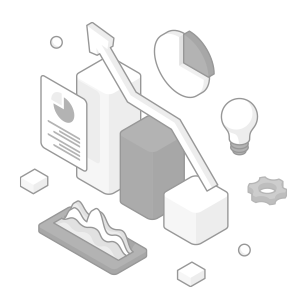
FAQs zur Batterie-Beschriftung in der Elektrofahrzeugindustrie
Welche Laser bietet KEYENCE zur Batterie-Beschriftung?
KEYENCE bietet eine breite Palette von Lasersystemen. Für die Beschriftung von Batterien sind UV- und Hybrid-Laser ideal.
- MD-X-Laser: Hybridlaser für präzise und dauerhafte Markierungen
- MD-U-Laser: UV-Laser für empfindliche Materialien
Was sind die Vorteile der Laserbeschriftung mit KEYENCE?
Folgende Vorteile bietet eine Laserbeschriftung von Batterien mit KEYENCE:
- Dauerhaftigkeit: Widersteht Hitze, Chemikalien und Abrieb.
- Präzision: Hochauflösende Markierungen, selbst auf kleinsten Flächen.
- Nachhaltigkeit: Keine Verbrauchsmaterialien wie Tinte oder Etiketten.
- Flexibilität: Anpassbar an verschiedene Materialien wie Kunststoff oder Metall.
- Fälschungssicherheit: Manipulationssicher, da sie sich nicht entfernen lassen, ohne das Produkt zu beschädigen.
- Effizienz: Schnelle Verarbeitung ohne Werkzeugwechsel.
- Konformität: Erfüllt internationale Normen wie ISO 9001 und andere branchenspezifische Anforderungen.
Was bedeuten die Angaben auf der Batterie?
Die Angaben auf einer Batterie geben wichtige Informationen wie die Kapazität (z. B. mAh), die Spannung (z. B. V), die chemische Zusammensetzung (z. B. Lithium-Ionen) und Sicherheitskennzeichnungen an. Diese Daten sind essenziell für die Rückverfolgbarkeit, den sicheren Betrieb und die Kompatibilität.
Welche Kennzeichnungen stehen auf der Batterie?
Typische Kennzeichnungen auf Batterien umfassen:
- Technische Daten: Kapazität, Spannung, Ladezyklen
- Herstellerangaben: Name, Logo, Seriennummer
- Sicherheitsinformationen: Warnhinweise, Recycling-Symbole, CE-Kennzeichnung
- Rückverfolgbarkeitsdaten: 2D-Codes, Seriennummern oder QR-Codes
Wie müssen Batterien gekennzeichnet werden?
Die Batterie-Beschriftung muss gut lesbar, dauerhaft und fälschungssicher sein. Rückverfolgbarkeitsinformationen, wie Seriennummern oder 2D-Codes, sind ebenfalls vorgeschrieben.
Was bedeuten die Buchstaben auf Batterien?
Die Buchstaben geben meist die Bauform und chemische Zusammensetzung an und helfen bei der Identifikation und richtigen Anwendung der Batterie. Zum Beispiel:
- AA/AAA: Größe und Form
- Li-Ion: Lithium-Ionen-Technologie
- NiMH: Nickel-Metallhydrid-Batterie