Koordinatenmessgeräte
Koordinatenmessgeräte
Unsere tragbaren 3D-Koordinatenmessgeräte ermöglichen eine einfache Messung von 3D- und F<-Merkmalen, Vergleiche mit CAD-Daten und eine automatische Erstellung detaillierter Prüfberichte – auch direkt in der Produktion. Der handgeführte Messtaster ermöglicht eine leichte Handhabung und uneingeschränkte Bewegungsfreiheit und bietet gleichzeitig die Möglichkeiten und die Genauigkeit eines 3D-Koordinatenmessgeräts.
Produktpalette
Das 3D-Fertigungsmesssystem schließt die Lücke zwischen großen Messgeräten und Handmessmitteln. Durch die intuitive Bedienung kann jeder Benutzer ganz einfach Form-und Lagetoleranzen direkt in der Fertigung durchführen. Das kompakte und portable Design erlaubt es das Gerät überall, standortunabhängig einzusetzen. Nach jeder Messung wird automatisch ein Prüfbericht mit Bildern erstellt. Zudem kann mit 3D-CAD-Daten gemessen werden. Die Bilder zeigen unser neuestes Modell XM-5000, das hochpräzise Messungen für handflächengroße Teile bis hin zu großen Bauteilen ermöglicht.
Merkmale
Hochpräzise 3D-Messung mit einem handgeführten Messtaster
Die Messobjekte können aus jedem Winkel gemessen werden, was eine intuitive Messung ermöglicht. Die auf dem Monitor angezeigten Messergebnisse sind einfach zu verstehen und enthalten Bilder zur besseren Veranschaulichung.
Großflächige Messung mit einem maximalen Messbereich von 2 m
Das Messvolumen ist 66 Mal größer als bei bisher eingesetzten Modellen. Von handflächengroßen Teilen bis hin zu großen Bauteilen kann alles gemessen werden.
Horizontaler Messbereich
Vertikaler Messbereich
Die Mobilen 3D-Koordinatenmessgeräte der Modellreihe WM können die Abmessungen und Formen von Produkten problemlos messen. Abmessungen können mit dem Messtaster und Formen mit dem Laser-Scanner gemessen werden. Die kabellosen Messtaster sorgen für einen uneingeschränkten Einsatz und ermöglichen so eine einfache Messung über einen großen Bereich. Da keine Vorbereitung wie Sprühen oder Kleben von Referenzpunkten erforderlich ist, kann das Scannen schnell und mit hoher Genauigkeit durchgeführt werden.
Merkmale
Kabellos Messen und Scannen
Messarme / Handgeführte Messgeräte / Lasertracker
Schwierige Handhabung
- Begrenzte Messmöglichkeiten
- Vorsicht bei der Montage des Geräts erforderlich
- Erfahrung mit Messungen erforderlich
WM Modellreihe
Einfache Messung mit kabellosen Messtastern
- Überall einsetzbar ohne Einschränkungen bei der Messung
- Großer Messbereich
- Sofort einsetzbar, auch für ungeübte Anwender
Schnelle ortsunabhängige Messung
Die tragbare Größe ermöglicht bei Bedarf eine schnelle Messung vor Ort.
Ein 3D-Koordinatenmessgerät (KMG) ist ein Messgerät, das die Geometrie von Objekten misst, indem es mithilfe eines Messtasters diskrete Punkte auf einer physischen Oberfläche festlegt. Das Gerät gibt die Position des Messtasters in Bezug auf die Verschiebung von einem Ursprungspunkt in einem dreidimensionalen Koordinatensystem (XYZ-Achsen) an. Ein KMG kann kritische 3D-Abmessungen mit hoher Genauigkeit messen, die gemessenen Daten aufzeichnen und komplexe Merkmale für Form- und Lagetoleranzen gewinnen. Berührungslose Modelle verwenden andere Methoden wie Kameras und Laser.
Teile eines 3D-Koordinatenmessgeräts (KMG)
Typischerweise sind die meisten 3D-Koordinatenmessgeräte Brücken- oder Portal-Modelle, wie in der Abbildung zu sehen. Der kugelförmige Kontaktpunkt, der an der Spitze des Messtasters angebracht ist, wird auf das Messobjekt auf dem Objekttisch aufgesetzt und die Koordinatenwerte in drei Dimensionen (X, Y, Z) werden festgelegt und gemessen.
Es wird hauptsächlich für die dreidimensionale Vermessung von Formen wie Automobilteilen und verschiedenen mechanischen Teilen, dreidimensionalen Objekten wie Prototypen und die Messung von Abweichungen von Zeichnungen verwendet.
A: Bewegliche Brücke, B: Trigger-Messtaster, C: Objekttisch, D: Steuergerät

- 2x
- 1.75x
- 1.5x
- 1.25x
- 1x, ausgewählt
- 0.75x
- 0.5x
- Kapitel
- Beschreibungen aus, ausgewählt
- Untertiteleinstellungen, öffnet Einstellungen für Untertitel
- Untertitel aus, ausgewählt
- en (Main), ausgewählt
This is a modal window.
Anfang des Dialogfensters. Esc bricht ab und schließt das Fenster.
Ende des Dialogfensters.
This is a modal window. Durch Drücken der Esc-Taste bzw. Betätigung der Schaltfläche "Schließen" wird dieses modale Fenster geschlossen.
Vorteile von 3D-Koordinatenmessgeräten (KMGs)
Im Gegensatz zu Handwerkzeugen wie Mikrometern, Messschiebern oder Höhen-/Tiefenmessern, welche jeweils nur in eine Richtung messen können, bieten 3D-Koordinatenmessgeräte (KMGs) die Möglichkeit der dreidimensionalen Messung in X-, Y- und Z-Richtung.
3D-Koordinatenmessgeräte verfolgen eine Tastspitze präzise im 3D-Raum und erzeugen dimensionale Messungen durch Formbildung über die Punkte, die durch Kontakt mit dem Messobjekt erfasst werden. Eine noch größere Anzahl von Punkten kann über eine größere Fläche auf dem Objekt erfasst werden, um die Oberfläche abzubilden und mit CAD-Daten zu vergleichen, die zur Prüfung von Formen, Wölbungen und Biegungen herangezogen werden.
Ein großer Vorteil von 3D-Koordinatenmessgeräten (KMGs) besteht darin, dass sie Gegenstände, die mit anderen Messgeräten schwer zu messen sind, mit hoher Genauigkeit messen können.
Ein weiteres Merkmal, das sich aus dem CNC-Charakter des Messsystems ergibt, ist die Möglichkeit, die dreidimensionalen Koordinaten eines bestimmten Punkts (einer Bohrung usw.) vom virtuellen Ursprung aus mit einem Handwerkzeug wie einem Messschieber oder einer Messschraube zu messen. Die Messung mit virtuellen Punkten und virtuellen Linien sowie geometrische Toleranzen erweisen sich bei der Verwendung anderer Messmaschinen als herausfordernd, während sie mit einem 3D-KMG problemlos durchgeführt werden können.
3D-Koordinatenmessgeräte (KMGs) sind automatisierte Prüfwerkzeuge. Erfahrene Programmierer erstellen eine Messroutine oder ein Programm, indem sie alle erforderlichen 3D-Maße sowie Maße von Form- und Lagetoleranzen an einem Teil messen.
Sobald das Programm registriert und ein Ursprungspunkt durch ein Koordinatensystem festgelegt ist, können die Objekte platziert und mit dem 3D-Koordinatenmessgerät automatisch gemessen werden. Während in die Programmerstellung viel Zeit investiert wird, kann die eigentliche Prüfung des Objekts automatisch durchgeführt werden.
Lassen Sie das Messobjekt vor der Messung mindestens 5 Stunden lang im Messlabor, damit es sich an die Raumtemperatur (in der Regel 20°C) anpassen kann. Dadurch werden Messfehler und Diskrepanzen aufgrund von thermischer Ausdehnung vermieden.
Die Messungen werden durchgeführt, indem der Messtaster manuell oder mit einem Steuer-PC an die gewünschte Messstelle geführt wird. Das KMG zeichnet daraufhin die X-, Y- und Z-Koordinaten der Messtasterposition auf. Im Anschluss an die Aufnahme der Punkte erfolgt eine Berechnung spezifischer Maße durch die Systemsoftware. Dazu zählen unter anderem Durchmesser, Längen, Winkel sowie weitere kritische Maße.
Taststift-Kalibrierung (Messtaster-Kalibrierung)
Die Kalibrierung des Taststifts (Messtasters), der mit dem Objekt in Berührung kommt, ist aus zwei Gründen erforderlich, um eine exakte Messung zu gewährleisten. Erstens müssen die Koordinaten des sphärischen Mittelpunkts des Taststifts erkannt werden. Zweitens wird der Durchmesser der Taststiftkugel eingestellt. Durch die Festlegung des Durchmessers ist eine Verschiebung des Radius von dem Punkt, der die Kugel tatsächlich berührt (außerhalb der Kugel), zu den Koordinaten des Kugelmittelpunkts möglich.
Zur Kalibrierung wird in der Regel eine Kugel mit bekannter Sphärizität, die so genannte Referenzkugel, verwendet.
Vorsichtsmaßnahmen bei der Handhabung
Obwohl einige Modelle Messungen in der Größenordnung von 0,1 μm durchführen können, sind die korrekte Verwendung und Verwaltung für die Messgenauigkeit von entscheidender Bedeutung.
Stellen Sie sicher, dass sich die beweglichen Teile während des Betriebs horizontal und vertikal bewegen. Verwenden Sie auch einen Messstandard oder ein ähnliches Objekt, um auf Anzeigefehler zu prüfen.
Um genaue Messungen durchführen zu können, ist es wichtig, dass sich die Temperatur des Messobjekts im Messlabor an die Raumtemperatur anpassen kann. Alternativ müssen die Messparameter so eingestellt werden, dass sie für jede Temperaturdifferenz korrigiert werden.
Bei Messtastern ist darauf zu achten, dass der Taster während der Messung mit konstanter Geschwindigkeit auf das Messobjekt trifft.
Wartung und Kalibrierung
Herkömmliche KMGs erfordern eine regelmäßige Wartung und Überprüfung, um eine kontinuierlich hohe Messgenauigkeit zu gewährleisten. Insbesondere bei Brücken-KMGs, deren Antriebssystem auf gleitenden Teilen basiert, ist eine regelmäßige Wartung unerlässlich, um eine optimale Leistung sicherzustellen. Dazu gehören der Austausch verschlissener Teile, die Schmierung der Gleitflächen sowie die Reinigung des Systems.
Schulung für Bediener von 3D-Koordinatenmessgeräten (KMG)
Der sorgfältige Umgang mit 3D-Koordinatenmessgeräten erfordert in der Regel fortgeschrittene Bedienerfähigkeiten. KMG-Programmierer sind in der Regel hochqualifizierte Messtechniker.
KMG-Programmierer sind nicht nur für eine ordnungsgemäße Prüfung erforderlich, sondern auch für die sachgemäße Verwendung der KMGs, da die falsche Handhabung mit hohen Reparaturkosten verbunden ist. Aus diesem Grund sind hauptberufliche Prüfer erforderlich, deren umfassende Ausbildung eine grundlegende Voraussetzung für den Betrieb darstellt.
Anwendungsbereiche von 3D-Koordinatenmessgeräten (KMGs)
Luft- und Raumfahrt und Verteidigungsindustrie
Siehe Fallstudien und Whitepaper von Luft- und Raumfahrt- sowie Verteidigungsunternehmen. Die integrierte SPC-Software des Systems sammelt automatisch Daten und erstellt detaillierte Prüfberichte, um die Anforderungen der AS9100 zu erfüllen. Zu den Anwendungsbeispielen gehören präzisionsbearbeitete Komponenten, Gussteile, Formteile und Baugruppen.
Maschinenbetriebe
Siehe Fallstudien und Whitepaper von kleinen bis mittelgroßen Maschinen- oder Lohnfertigungsbetrieben. Ganz gleich, ob hochpräzise Komponenten benötigt werden, die die Präzision eines 3D-Koordinatenmessgeräts (KMG) benötigen, oder ob Prüfer und Maschinenführer in der Lage sein sollen, Teile in der Fertigung blitzschnell zu prüfen – die Modellreihe XM ist das richtige Werkzeug für diese Aufgaben.
Eingangsprüfung
Siehe Literatur, in der untersucht wird, wie die Prüfeffizienz verbessert und die Eingangsprüfung schneller abgeschlossen werden kann. Beispiele hierfür sind 3D-Koordinatenmessgeräte (KMGs) zur Verhinderung von Engpässen durch die schnelle Objektprüfung durch jedermann und überall in der Produktionsstätte.
Taststift/Messtaster
In der Regel weisen die Taststifte von KMGs einen kugelförmigen Durchmesser auf. An der Spitze der Messtaster werden häufig harte Materialien verwendet – am häufigsten Rubin und Zirkondioxid.
Des Weiteren besteht die Möglichkeit, anstelle der Kugelform einen Nadeltyp mit einer scharfen Spitze zu verwenden.
Granit-Tisch
Die Oberfläche eines 3D-Koordinatenmessgeräts ist häufig aus einer Steinplatte gefertigt, um eine hochgenaue Messung zu gewährleisten. Die Steinoberfläche zeigt im Verlauf der Zeit nur eine geringe Veränderung ihrer Form und neigt nicht zur Bildung von Kratzern. Dies gewährleistet eine lange Nutzungsdauer.
Vorrichtungen
Eines der wichtigsten Hilfsmittel bei der Verwendung eines 3D-Koordinatenmessgeräts sind Vorrichtungen zur Fixierung eines Messobjekts.
Die Fixierung des Messobjekts ist erforderlich, um eine Bewegung desselben während des Betriebs des Koordinatenmessgeräts zu verhindern. Eine Bewegung des Messobjekts würde zu Fehlern bei der Messung führen. Zur Befestigung werden üblicherweise Werkzeuge wie Spannplatten, Klemmen und Magnete verwendet.
Luftkompressoren und -trockner
Mechanisch angetriebene 3D-Koordinatenmessgeräte benötigen einen Luftkompressor mit einem Trockner. Dies ist bei standardmäßigen Brücken- oder Portal-KMGs der Fall.
Software
Es gibt grob zwei Arten von Software für 3D-Koordinatenmessgeräte.
Die erste ist die für den Betrieb der Maschine erforderliche Software. Die zweite ist eine Software für die statistische Prozesskontrolle (SPC), mit der Unternehmen Messdaten und Statistiken anzeigen und überwachen können. Diese Softwarepakete kommen direkt vom KMG-Hersteller oder von einem Drittanbieter.
Messung des 3D-Koordinatenmessgeräts (KMG)
In der Regel ist bei KMGs ein Gerätekoordinatensystem fest definiert, welches sich auf das jeweilige Objekt bezieht.
Die Definition des Koordinatensystems erfolgt durch das Gerät selbst. Dabei wird die Richtung der Achse, welche eine seitliche Bewegung ausführt, als X-Achse bezeichnet. Die Richtung, welche senkrecht zur Oberfläche des Objekttisches verläuft, wird als Z-Achse definiert. Infolgedessen kann eine Abweichung von der Bezugsebene oder Bezugslinie des zu messenden Objekts erforderlich sein, abhängig von der Ausrichtung des zu messenden Objekts. Die physische Übertragung auf die Maschinenkoordinaten erweist sich als schwierig und ungenau, sodass das Arbeitskoordinatensystem entsprechend der Bezugsebene oder der Bezugslinie des Objekts festgelegt wird.
In der Folge wird eine Übereinstimmung zwischen der Ausrichtung des Objekts und der Ausrichtung der Referenzkoordinaten erzielt.
Zum Einstellen des Arbeitskoordinatensystems sind drei Informationen erforderlich.
Die erste ist die Ebene, die die Bezugsebene darstellt, und die Richtung senkrecht zu dieser Ebene ist die Z-Achse.
Die zweite ist die Bezugslinie, die im Allgemeinen die X-Achse und die vertikale Richtung die Y-Achse ist. Die gerade Linie kann direkt vom Objekt aus gemessen werden, oder sie kann eine gerade Linie sein, die zwei verschiedene Punkte (z. B. zwei Löcher) mit einer virtuellen Linie verbindet.
Die dritte ist der Bezugspunkt. Als Bezugspunkt für die X-, Y- und Z-Koordinatenwerte kann der jeweilige Nullpunkt herangezogen werden. Alternativ ist die Angabe eines bestimmten Punktes, etwa des Mittelpunktes einer Bohrung, oder eines virtuellen Punktes, wie des Schnittpunktes zweier Geraden, möglich.
In der Regel wählt der Benutzer über ein Softwaremenü ein „Element“ genanntes Messobjekt, z. B. eine Ebene, aus und beginnt mit der Messung. Bei einem 3D-Koordinatenmessgerät wird die Taststiftspitze mit dem zu messenden Objekt in Kontakt gebracht und der Messpunkt erfasst. Die Messung des Elements erfolgt durch die Erfassung der für jedes Element angegebenen Mindestanzahl von Messpunkten. Wird die Zahl der Messpunkte weiter erhöht, wird sie häufig nach der Methode der kleinsten Quadrate berechnet.
Zu den Messelementen gehören neben Ebenen auch Linien, Punkte, Kreise, Zylinder, Kegel und Kugeln.
Die Ermittlung von Abmessungen und 3D-Formen erfolgt durch die Berechnung von Abständen und Winkeln zwischen den gemessenen Elementen.
Einige Elemente weisen eine dreidimensionale Form auf, beispielsweise in Form eines Zylinders oder Kegels. Andere Elemente hingegen besitzen keine derartige Form, wie beispielsweise Linien oder Kreise. Diese Elemente werden in der Regel auf eine Ebene projiziert, wobei eine senkrechte Ausrichtung zur Ebene erfolgt, um eine korrekte Messung zu gewährleisten. Die projizierte Ebene wird als Bezugsebene oder Projektionsebene bezeichnet.
3D-Koordinatenmessgeräte können auch mit virtuellen Linien und Punkten messen.
Es werden verschiedene Beispiele für virtuelle Elemente verwendet, wie Schnittpunkte zwischen Geraden, Toleranzen zwischen Ebenen, Schnittpunkte zwischen Ebenen und Kreise zwischen Kegeln und Ebenen.
Man kann sagen, dass die Messung mit diesen virtuellen Elementen, die mit Handwerkzeugen wie einem Messschieber nur schwer zu messen ist, einzigartig für die 3D-Messung ist.
Probleme von 3D-Koordinatenmessgeräten (KMG)
Für die richtige Einstellung und Messung sind spezielle Kenntnisse und Fähigkeiten erforderlich.
Es ist erforderlich, eine adäquate Temperatur im Messraum zu gewährleisten und die Temperatur des Objekts zu stabilisieren.
Da bei jeder Änderung verschiedener Einstellungen und Messtaster-Winkel eine Kalibrierung erforderlich ist, ist es nicht einfach, häufige Produktwechsel zu bewältigen.
Die Notwendigkeit eines Messraums bedingt eine erschwerte Durchführung wiederholter Messungen während der Bearbeitung des Objekts.
Die Installation erfordert einen großen Raum und den Bau eines umgebungskontrollierten Qualitätslabors, was sehr teuer ist.
Die Kosten für die Instandhaltung der Messumgebung und der Messgeräte können eine Belastung darstellen.
Die Programmierung des KMG ist aus mehreren Gründen sehr zeitaufwendig. Die Zeit, die benötigt wird, um das Teil in das Qualitätslabor zu transportieren, es auf die richtige Temperatur zu bringen, es zu befestigen, jeden Messtaster zu kalibrieren und die Zeit, die benötigt wird, um die Messung durchzuführen.
Die Modellreihe XM von KEYENCE ist ein neuartiges 3D-Koordinatenmessgerät, das die Einschränkungen konventioneller KMGs überwindet. Es handelt sich um ein tragbares Tisch-KMG, mit dem jeder Bediener problemlos 3D- bzw. Form- und Lagetoleranzen-Merkmale messen kann. Das Gerät benötigt auch keine kontrollierte Umgebung und kann in der Produktion eingesetzt werden. Erfahren Sie mehr über dieses KMG der nächsten Generation!
Einfach in der Anwendung
So hilfreich ein Vorgänger-KMG auch sein mag, ein großer Nachteil ist die schwierige Bedienung. KEYENCE ist bestrebt, den Umgang mit KMGs durch die Einführung eines intuitiven Verfahrens zu erleichtern. Die Messung erfolgt in drei einfachen Schritten: auswählen, berühren und messen.
Sowohl die Modellreihe WM als auch die Modellreihe XM verfügen über eine visuelle Benutzerführung und einfache Tutorials, um Unklarheiten zu vermeiden. Sobald die Messung in die Software importiert wurde, werden zusätzliche Hinweise angezeigt. Die KMG-Programmierung von KEYENCE ist eine integrierte Software, die mit Bildern, Symbolen und grundlegenden Messverfahren arbeitet.
Vielseitig
Vorgänger-KMGs sind entweder sperrige Handgeräte oder Portal-Systeme, die für größere Objekte nicht geeignet sind. Die Modellreihen XM und WM von KEYENCE begegnen diesen beiden Problemen mit einem drahtlosen Messtaster und einem tragbaren System, das keine kontrollierte Umgebung benötigt.
Die KMGs der Modellreihe XM werden mit einem Messtisch für kleine Teile geliefert, das eigentliche KMG kann jedoch auch auf einem Stativ oder einer Stütze befestigt werden. Aufgrund seiner Tragbarkeit kann dieses KMG auch vom Messtisch abgenommen und problemlos für große Objekte verwendet werden.
Die Modellreihe WM ist tragbar und hilft bei der Messung großer Objekte und Baugruppen. Das Gerät kann an jedem gewünschten Messort aufgestellt und die Maßhaltigkeitsprüfung von großen Bauteilen kann von einer einzigen Person in kurzer Zeit durchgeführt werden.
Großer Bereich
Die KMGs von KEYENCE decken einen breiten Messbereich für eine Vielzahl von Objekten ab. Das 3D-Koordinatenmessgerät der Modellreihe XM bietet einen maximalen Messabstand von 1,2 m zur Kamera und 1 m vertikale Höhe. Das volle Sichtfeld der Kamera ermöglicht einen Messbereich von 2 m von einem Ende zum anderen. Mit diesem System wird ein großer Messbereich mit hoher Messgenauigkeit erreicht.
Die Modellreihe WM deckt einen noch größeren Bereich ab: bis zu 12,5 m in der Vertikalen und in der Horizontalen. Insgesamt erfasst das 3D-Koordinatenmessgerät der Modellreihe WM eine Länge von 25 m vom äußersten rechten Winkel bis zum äußersten linken Winkel.
Verwandte Produkte
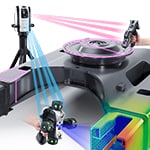
Der neue Lasertracker von KEYENCE ist mit einem speziellen kabellosen Messtaster ausgestattet, der die Bewegungsfreiheit bei der Messung großer Prüfobjekte nicht einschränkt. Die Messungen können praktisch überall durchgeführt werden, ohne dass die Prüfobjekte in ein Messlabor transportiert werden müssen, was dazu beiträgt, den Zeitaufwand für die Messungen zu verringern und die Betriebsraten zu verbessern. Darüber hinaus ist die Wiederholgenauigkeit sehr hoch – im μm-Bereich – wodurch Schwankungen der Messergebnisse bei Objekten mit komplexen Formen, die eine hohe Genauigkeit erfordern, wie z. B. Turbinenschaufeln, vermieden werden.
Die Ressourcen des KMGs
Auswahl eines KMGs
3D-Koordinatenmessgeräte (KMGs) sind effiziente und genaue Messwerkzeuge, die Messalternativen wie Maßstäbe, Mikrometer und Messschieber übertreffen. Diese vielseitigen Geräte messen die 3D-Maße, Form- und Lagetoleranz-Merkmale und vergleichen sie mit CAD in Branchen wie dem Gesundheitswesen, der Automobilindustrie, der Luft- und Raumfahrt und anderen.
Aber nicht alle KMGs sind gleich – was gut ist! KMGs verfügen über unterschiedliche Messbereiche, Softwares und Genauigkeiten. Jeder dieser Faktoren sollte bei der Auswahl des richtigen KMG für Ihre Prüf- oder Messanforderungen berücksichtigt werden.
Wenn Sie sich also fragen, wie Sie ein KMG auswählen sollen, wird Ihnen der folgende Beitrag helfen.
Tragbare vs. stationäre KMGs und Auswahl eines KMG
3D-Koordinatenmessgeräte (KMGs) sind unverzichtbare Werkzeuge für Messungen und Prüfungen in Branchen wie der Luft- und Raumfahrt, der Automobilindustrie und der Medizintechnik. Es gibt zwei Arten von KMGs, tragbare und stationäre, und jedes hat je nach Einsatzzweck seine Vorteile.
Bei der Entscheidung zwischen einem tragbaren und einem stationären KMG ist es wichtig, die zentralen Merkmale zu kennen, durch die sich die beiden unterscheiden. In diesem Beitrag gehen wir darauf ein, was ein KMG ausmacht, welche Vorteile ein stationäres KMG hat, welche Vorteile ein mobiles KMG hat und welche Anwendungen es gibt.
Lasertracker
KEYENCE bietet Lasertracker an; unsere tragbaren 3D-Koordinatenmessgeräte ermöglichen es jedem, auf einfache Weise 3D-/Form- und Lagetoleranz-Merkmale zu messen, mit CAD-Daten zu vergleichen und automatisch detaillierte Prüfberichte zu erstellen – überall, auch in der Produktion.
Messarme
Entdecken Sie die Messarm-Lösungen von KEYENCE. Erzielen Sie präzise Messungen mit der tragbaren und roboterarmgestützten Technologie. Optimieren Sie den Messprozess für präzises 3D-Messen.
Wie funktionieren Lasertracker?
Entdecken Sie die Leistungsfähigkeit des Lasertracking: Erfahren Sie, wie Lasertracker funktionieren und welche Rolle sie bei präzisen Messungen spielen. Erfahren Sie mehr über die Möglichkeiten von Lasertracking-Systemen und die Rolle der Bediener.
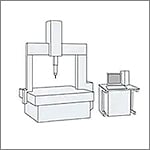
„Messgrundlagen“ ist eine informative Website, die Informationen über Maßhaltigkeitsprüfungen in der Fertigung bereithält, einschließlich der Grundlagen zu 3D-Koordinatenmessgeräten (KMG).
Häufig gestellte Fragen zu 3D-Koordinatenmessgeräte (KMGs)
3D-Koordinatenmessgeräte (KMGs) sind komplizierte Prüfwerkzeuge mit vielen beweglichen Teilen, temperatur- und feuchtigkeitsempfindlichen Komponenten und verschiedenen zerbrechlichen Elementen. In rauen Produktionsumgebungen, in denen ein viel höheres Potenzial für kostspielige Schäden oder nicht optimale Messbedingungen besteht, kann es zu Ungenauigkeiten bei der Prüfung kommen. Messlabore sind als Sicherheitszonen konzipiert, die von der Produktion abgeschottet sind; sie bieten optimale Bedingungen für eine ordnungsgemäße Prüfung.
Das 3D-Fertigungsmesssystem der Modellreihe XM von KEYENCE ist ein tragbares 3D-Fertigungsmesssystem für den direkten Einsatz in der Produktion, das es jedem Anwender ermöglicht, 3D-Merkmale sowie Merkmale von Form- und Lagetoleranzen einfach und präzise zu messen – überall und jederzeit. Wenn das Teil gemessen wird, zeichnet das System die Daten automatisch auf und erstellt einen Prüfbericht. Unser neuestes Gerät ermöglicht den CAD-Vergleich und den 3D-CAD-Export. Im Vergleich zu den bisher eingesetzten 3D-Koordinatenmessgeräten (KMGs) erreichen Unternehmen eine erhebliche Reduzierung der Prüfzeit und einen erhöhten Durchsatz durch Prüfungen direkt in der Produktion durch jedermann, sodass jeglicher Rückstand beim 3D-Koordinatenmessgerät (KMG) abgebaut werden kann.
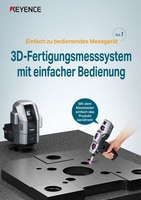

Siehe gängige Anwendungsbeispiele für 3D-Koordinatenmessgeräte, die mit dem Handmessgerät der Modellreihe XM gemessen wurden. Zu den Anwendungsbeispielen gehören: Drehteile, zerspante Teile, Stanzteile, Gussteile und Formteile.

Lesen Sie hier, wie Sie Maßhaltigkeitsprüfungen in der Fertigung durchführen und welche Messmittel Sie für die unterschiedlichen Messaufgaben benötigen. Erfahren Sie mehr über die Grundlagen von Profilprojektoren und 3D-Koordinatenmessgeräten.