Prüfung von Qualitätsmerkmalen
Erkennung von Fremdkörpern, Mängeln, Verunreinigungen und Defekten
Bei der Qualitätskontrolle wird auf Fremdkörper, Werkstofffehler und Defekte an der Oberfläche von Teilen oder Produkten geprüft. Typische zu prüfende Qualitätsmerkmale:
- Überprüfung von Lebensmittelverpackungen auf Fremdkörper
- Prüfung auf Flecken auf Stoff
- Prüfung auf Werkstofffehler an Metall-/Kunststoffbauteilen
- Prüfung auf Mängel wie Absplitterungen oder durch den Formprozess von Kunststoff/Gummi entstandene Grate
- Mängelprüfung an ausgeschalteten LEDs
In der Vergangenheit bestand die Prüfung von Qualitätsmerkmalen in einer reinen Sichtprüfung. Als Folge der zunehmenden Automatisierungstechnik kommen zunehmend Bildverarbeitungssysteme zum Einsatz. Auf dieser Seite werden die Anwendungsfelder der Bildverarbeitung beschrieben, in denen sich Produkte besser auf Fremdkörper, Werkstofffehler und Defekte prüfen lassen. Zusätzlich werden die Grundprinzipien und die neuesten Trends in der Qualitätskontrolle vorgestellt.
Grundprinzip der Qualitätskontrolle bei der Erkennung von Fremdkörpern, Werkstofffehlern sowie Defekten anhand von Bildern
Vorteile der Einführung von Bildverarbeitungssystemen
Winzige Werkstofffehler oder Verfärbungen sind schwer auszumachen, so dass die Bilder mit Mikroskopen vergrößert werden müssen, um die Qualität zu sichern. Bei einer begrenzten Anzahl von Objekten können Prüfungen mit dem Mikroskop noch außerhalb der Linie durchgeführt werden. Geht die Zahl der Objekte allerdings in die Tausenden oder Zehntauschenden, ergibt sich daraus ein erheblicher Arbeitsaufwand, der wiederum erhebliche Effizienzeinbußen mit sich bringt. Sollen unter diesen Bedingungen sowohl hohe Qualität als auch hohe Effizienz gewährleistet werden, führt an der Bildverarbeitung kein Weg mehr vorbei.
Zuverlässige Erkennung von winzigen Fremdkörpern, Werkstofffehlern und Defekten
Kunden, die über die Einführung von Bildverarbeitungssystemen nachdenken, fragen häufig, wie groß Fremdkörper oder schwarze Punkte mindestens sein müssen, damit sie bei der Prüfung noch erfasst werden können. Die ungefähre Größe lässt sich anhand der unten stehenden Formel berechnen.
Kleinste erkennbare Größe = B / A × C
- A: Anzahl der Punkte des Bildaufnahmeelements in Y-Richtung
- B: Bildfeld (Y-Richtung) [mm]
- C: Minimale Anzahl an Punkten auf dem Bildaufnahmeelement, mit der ein Messobjekt erfasst werden kann [Pixel]
Die Anzahl der Punkte variiert je nach eingesetzter Kamera. So verfügt beispielsweise eine 0,31-Megapixel-Kamera über 480 vertikale Punkte, eine 21-Megapixel-Kamera dagegen über 4.092. Dieser Wert entspricht [A: Anzahl der Punkte des Bildaufnahmeelements in Y-Richtung] in der Berechnungsformel.
Element B, das Bildfeld (Y-Richtung), kann durch Wechsel des Objektivs auf 10 mm, 100 mm oder jeden anderen Wert angepasst werden. Element C, die minimale Anzahl an Punkten auf dem Bildaufnahmeelement, mit der ein Messobjekt erfasst werden kann, sollte im Normalfall auf 3 Punkte und unter besonders schweren Bedingungen auf 5 Punkte gesetzt werden.
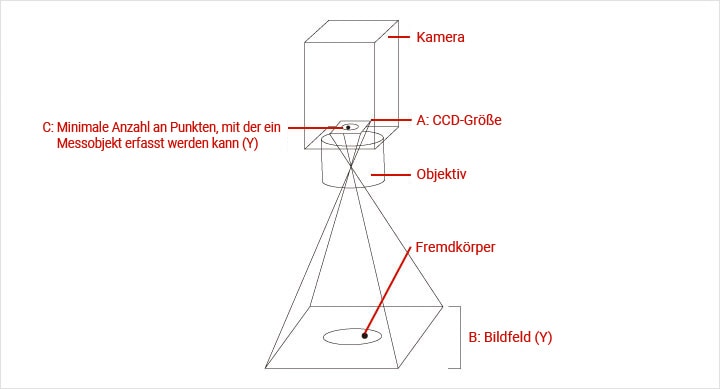
Unter den obigen Bedingungen, wenn A = 480 Pixel, B = 50 mm und C = 3 Pixel, lautet die Berechnung:Kleinste erkennbare Größe =50 / 480 × 3 = 0,312 mmDas bedeutet, dass Fremdkörper oder Werkstofffehler von gerade einmal 0,312 mm bei der Prüfung noch erkannt werden.
Für eine 21-Megapixel-Kamera lautet die Berechnung:Kleinste erkennbare Größe =50 / 4.092 × 3 = 0,037 mmFremdkörper oder Werkstofffehler von gerade einmal 0,037 mm, die mit bloßem Auge kaum auszumachen sind, werden damit noch erkannt.
Für noch größere Prüfgenauigkeiten lässt sich die kleinste erkennbare Größe mithilfe einer hochauflösenden Kamera wie dem 21-Megapixel-Modell oder durch Reduzierung des Sichtwinkels weiter verringern.
Ermöglicht die 100%-Inspektion in der Linie
Je nach Prüfpunkt müssen Sichtprüfungen häufig außerhalb der Linie vorgenommen werden. Mit der Bildverarbeitung dagegen sind auch Inline-Prüfungen auf Fremdkörper, Werkstofffehler und Defekte möglich.
Abhängigkeit zwischen Messobjekt- und Verarbeitungsgeschwindigkeit
Vereinzelte Beschickung
Mithilfe dieser Formeln lässt sich die maximale Anzahl von Prüfungen pro Minute sowie die Geschwindigkeit für die Bildverarbeitung ermitteln, wenn das Transportmittel jeweils für eine bestimmte Zeit angehalten wird, damit das nächste zu prüfende Objekt vor der Kamera präsentiert werden kann.

Maximale Anzahl an Prüfungen pro Minute = 60 Sekunden/ Verarbeitungszeit durch das Bildverarbeitungssystem in Sekunden
Beispiel: Bei einer Verarbeitungsgeschwindigkeit des Bildverarbeitungssystems von 20 ms
60 Sekunden/0,02 Sekunden = 3.000 Mal/Minute (50 Mal/Sekunde)
Eine einfache Qualitätsprüfung kann innerhalb von ca. 20 bis 100 ms verarbeitet werden. Wenn Sie die gewünschte Prüfgeschwindigkeit kennen, können Sie die erforderliche Verarbeitungsgeschwindigkeit anhand der folgenden Formel berechnen:
Vom Bildverarbeitungssystem geforderte Verarbeitungsgeschwindigkeit (ms) = 1/gewünschte Anzahl der Prüfungen pro Sekunde × 1.000
Beispiel: Bei einer Sollanzahl von Prüfungen von 50 Mal/ Sekunde
1 / 50 × 1000 = 20 ms
Anhand der oben genannten Formel kann man dann ein Bildverarbeitungssystem auswählen, das auf die jeweiligen Anforderungen zugeschnitten ist. Dabei ist zu beachten, dass diese Berechnung nur für die vereinzelte Beschickung gilt. Bei einer kontinuierlichen Beschickung, wenn die Produkte ohne Halt durchlaufen, muss auch die Belichtungszeit berücksichtigt werden.
Kontinuierliche Beschickung
Bei kontinuierlicher Beschickung muss entsprechend der Bandgeschwindigkeit eine passende Belichtungszeit gewählt werden. Andernfalls erscheint die Bildaufnahme verschwommen und es ist keine präzise Prüfung möglich. Im Allgemeinen wird die Geschwindigkeit so gewählt, dass der Verfahrweg etwa einem Fünftel der kleinsten erkennbaren Objektgröße entspricht.
Beispiel: Die gewünschte kleinste erkennbare Größe ist 1 mm, und die Bandgeschwindigkeit liegt bei 1 m/Sekunde
Referenzbelichtungszeit = 1 (mm) / 5 / 1.000 (mm/s) = 1/5.000 Sekunde
Grundlagen der Qualitätsprüfung: Bildaufbereitungsfilter
Bei der Prüfung von Qualitätsmerkmalen müssen kleinste Werkstofffehler und Absplitterungen erkannt und unterschieden werden. Bildaufbereitungsfilter tragen wesentlich zur Erreichung stabiler Prüfergebnisse bei.
Kontrastkorrektur
Wie im Abschnitt über die Anwesenheitsprüfung beschrieben, war die Binärverarbeitung bei der Suche nach Fremdkörpern oder Werkstofffehlern nur bedingt einsetzbar. Mit der Kontrastkorrektur lassen sich Glanzeffekte oder Schatten an der Oberfläche eines Messobjekts ausgleichen, um Flecken oder Fehler erfolgreich extrahieren zu können.

Ursprüngliches Bild


Nach der Bildaufbereitung
Bidirektionaler Glättungsfilter
Haarrisse oder andere Hintergrundmuster sowie Rauschen können mit diesem Filter entfernt werden. Der Glättungseffekt kann für die X- und die Y-Richtung separat eingestellt werden. Mit diesem Filter lassen sich ausschließlich Fremdkörper extrahieren.

Ursprüngliches Bild


Nach der Bildaufbereitung
Blob-Filter
Mit diesem Filter wird das Bild einer Blob-Analyse unterzogen, die im Abschnitt über die Anwesenheitsprüfung beschrieben ist. Damit lassen sich nur spezifische Faktoren extrahieren, indem Glanzeffekte, Schatten, Hintergründe und Unebenheiten in der Oberfläche ausgeblendet werden.

Kontrastkonvertierung
Mit diesem Filter wird ein Bild mit dem bestmöglichen Kontrast erzeugt, um Kanten stärker herauszuarbeiten und mögliches Hintergrundrauschen zu unterdrücken. Durch eine Erweiterung der Kontrastabstufungen lassen sich Flecken und andere Defekte leichter erkennen.
Praktische Anwendungen
Die Bildverarbeitung wird bei den unterschiedlichsten Qualitätsprüfungen bereits erfolgreich eingesetzt. Im Folgenden haben wir für Sie einige Anwendungsbeispiele zusammengestellt.
Inspektion auf Schleifstaub an Kolben
Schleifstaub auf den Kolben von Fahrzeugmotoren ist mit bloßem Auge kaum erkennbar und wird bei der Sichtprüfung häufig übersehen. Mithilfe von Bildverarbeitungssystemen kann mikroskopisch kleiner Schleifstaub präzise erkannt und unterschieden werden.

Prüfbildschirm


Schleifstaub
Prüfung von Chip-Kondensatoren auf unterschiedliche Defekte
Dank des Einsatzes von Bildverarbeitungssystemen können Chip-Kondensatoren zeitgleich auf unterschiedliche Defekte wie Flecken, Werkstofffehler und Absplitterungen geprüft werden. Zuverlässige 100%-Inspektionen sind möglich! Durch die Auswertung der gesammelten Prüfdaten lassen sich Abläufe stetig verbessern.
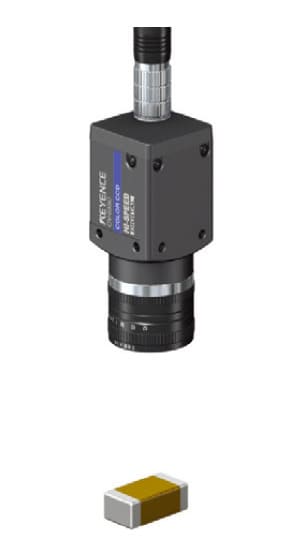
Prüfbildschirm


Prüfung auf Fremdkörper in Transportbehältern
In dem Maße, wie das Thema Nahrungsmittelsicherheit immer stärker ins Zentrum der Aufmerksamkeit rückt, hat auch die Nachfrage nach Bildverarbeitungssystemen in der Nahrungsmittelindustrie zugenommen. Transportbehälter wurden bislang nur stichprobenartig auf Fremdkörper geprüft. Mit der Bildverarbeitung ist ohne Zusatzaufwand eine 100%-Inspektion möglich. Dabei können auch winzige Flecken erkannt werden, wodurch gleichbleibende Qualität gewährleistet werden kann.
