Messung des Biegeradius bei der Blechbearbeitung

Beim Biegen von Metallwerkstoffen wird die Verformbarkeit (Duktilität) genutzt, die Metallen eigen ist. Sie ist eine Bearbeitungsmethode, die häufig in der Blechbearbeitung und anderen Metallbearbeitungen eingesetzt wird.
Das Biegen steht in engem Zusammenhang mit der Festigkeit eines Materials. Daher kann das Biegen in einem ungeeigneten Radius zu Verformungen, verminderter Festigkeit und Beschädigungen führen. Aus diesem Grund kann die Messung des Biegeradius einen großen Einfluss auf die Qualität haben.
Auf dieser Seite werden am Beispiel der Blechbearbeitung grundlegende Kenntnisse über den Biegeradius, seine Berechnung, Gegenmaßnahmen bei Fehlern, Herausforderungen bei gängigen Messungen des Biegeradius und die neueste Messmethode erläutert, die die Arbeitseffizienz und -präzision erheblich verbessert.
- Biegeradius
- Biegen in der Blechbearbeitung
- Spannung beim Biegen in der Blechbearbeitung und entsprechende Vorsichtsmaßnahmen
- Berechnung der entwickelten Biegelänge anhand des Biegeradius
- Maßnahmen gegen Rissbildung und kleinster Biegeradius
- Herausforderung bei gängigen Messungen von Biegeradien
- Lösung von Herausforderungen bei der Messung von Biegeradien
- Zusammenfassung
Biegeradius
Der Biegeradius ist der Radius vom Startpunkt der Biegung bis zur Mitte der Biegung bei der plastischen Bearbeitung eines Metalls oder eines anderen Blechs, Rohrs oder Stabes durch Pressen oder Walzen.
Jedes Material hat eine Grenze für die Biegung ohne Bruch, die durch seine Dicke oder seinen Durchmesser bestimmt wird. Diese Grenze nennt man den kleinsten Biegeradius. Der Biegeradius muss auf die Biegeposition und die Anwendung abgestimmt werden. Die durch das Biegen verursachte Widerstandsspannung kann auch den fertigen Biegeradius beeinflussen.
Biegen in der Blechbearbeitung
Ein typischer Prozess, bei dem der Biegeradius wichtig ist, ist die Blechbearbeitung. Eine gängige Methode zum Biegen von Blechen verwendet eine so genannte Abkantpresse, die das Blech zwischen der oberen Matrize, dem so genannten Stempel, und der unteren Matrize, auch Untergesenk genannt, presst. Zusätzlich zu den in den folgenden Abbildungen gezeigten V-Matrizen werden je nach Biegeform und Material verschiedene Arten von Matrizen verwendet. Dazu gehören Radiusstempel, die das Blech in einer sanften Kurve biegen, und U-Biegestempel, die ein Blech an zwei Punkten gleichzeitig in einem Hub biegen.
- A
- Stempel (obere Matrize)
- B
- Blech
- C
- Untergesenk (untere Matrize)
- D
- Press- bzw. Biegevorgang
Beim Biegen von dicken Blechen verwenden einige Abkantpressen einen Radiusstempel oder eine tiefe V-Matrize (untere Matrize), auch beim normalen V-Biegen. Beim Biegen mit einem großen Biegeradius kann das Blech während des Biegens nach und nach verschoben werden. Zur Messung des Radius kann ein Stempel verwendet werden, der „Radiuslineal“ genannt wird.
Spannung beim Biegen in der Blechbearbeitung und entsprechende Vorsichtsmaßnahmen
Die folgenden Spannungen werden in einem gebogenen Blech erzeugt. Je nach Dicke und Härte des bearbeiteten Materials können diese Spannungen einen großen Einfluss auf den Biegeradius haben.
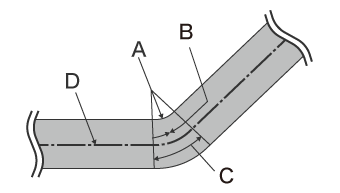
- A
- Biegeradius
- B
- Druckspannung
- C
- Zugspannung
- D
- Neutrale Achse
- • Druckspannung
- Die Innenseite der neutralen Achse der Blechdicke wird zusammengedrückt, wodurch eine Kraft im Material erzeugt wird, die der Kompression widersteht.
- • Zugspannung
- Die Außenseite wird in die Zugrichtung gedehnt, wodurch eine Kraft im Material erzeugt wird, die der Spannung widersteht.
- * Im Querschnitt in Dickenrichtung wird die durch die Mitte des Blechs verlaufende Linie, auf die keine dieser Kräfte einwirkt, als neutrale Achse bezeichnet.
Wenn das gepresste Material aus den Matrizen entnommen wird, kann das Material aufgrund der verbleibenden Druck- und Zugspannung zurückfedern, wodurch sich der Biegewinkel des gebogenen Teils vergrößert. Dies wird als Rückfederung bezeichnet und tritt eher bei harten Materialien auf, da diese dazu neigen, höhere Druck- und Zugspannungen zu erzeugen. Solche Materialien müssen in einem Winkel gebogen werden, der kleiner ist als der beabsichtigte Endwinkel.
Das Ausmaß der Rückfederung variiert je nach Blechmaterial und -dicke. Bei dicken Blechen ist die neutrale Achse tendenziell nach innen verschoben. Aus diesem Grund ist es wichtig, das Ausmaß der Rückfederung zu ermitteln und geeignete Bedingungen für die Metallbearbeitung festzulegen.
Berechnung der entwickelten Biegelänge anhand des Biegeradius
Die entwickelte Biegelänge wird benötigt, um eine stabile Biegung zu ermöglichen. Sie kann geschätzt werden, indem der Abstand von der Oberfläche des Biegeradius zur neutralen Achse ermittelt wird. Da die geraden Teile A und B durch das Biegen nicht verändert werden, verwenden Sie die tatsächlichen Werte.
Das Verschiebungsverhältnis der neutralen Achse (λ: Lambda) an einem gebogenen Punkt hängt von der Materialstärke, der Härte, dem Biegewinkel und dem inneren Biegeradius ab. Man geht davon aus, dass sich die neutrale Achse an einer Stelle befindet, die etwa 20% bis 45% der Dicke von der inneren Oberfläche entfernt ist. Am Arbeitsplatz werden Werte verwendet, die auf Erfahrung beruhen. Die Formel zur Berechnung der entwickelten Biegelänge ist wie folgt:

- a
- Abstand von der Oberfläche des Biegeradius zur neutralen Achse
- b
- Biegeradius
- c
- Neutrale Achse am gebogenen Teil
L = A + B + (R + T x λ) x 2n x θ / 360
L = Entwickelte Länge
A, B = Länge der Teile, die keiner Biegespannung ausgesetzt sind
R = Innerer Biegeradius
T = Dicke
θ = Biegewinkel
λ = Verschiebungsverhältnis der neutralen Achse (%) * Erfahrungswert
Maßnahmen gegen Rissbildung und kleinster Biegeradius
Zu den Herausforderungen, die beim Biegen auftreten, gehören Defekte wie Rissbildung und Ausreißen an den gebogenen Teilen. Achten Sie auf die Richtung, in der das Material bearbeitet wird, da diese Defekte eng mit der Walzrichtung des Materials zusammenhängen. Risse und andere Defekte treten mit größerer Wahrscheinlichkeit auf, wenn das Material parallel zur Walzrichtung gebogen wird. Diese Defekte treten besonders häufig bei Materialien aus rostfreiem Stahl und Aluminium auf.

- A
- Ort, an dem es wahrscheinlich zu Rissen kommt
- B
- Biegelinie
- C
- An der Biegelinie ausgerichtete Konturlinie
- D
- Walzrichtung parallel zur Biegelinie

- E
- Reduzierte Blechdicke am gebogenen Teil
- F
- Biegelinie
- G
- Querschnitt einer Bruchstelle
- H
- Biegebreite weniger als das Achtfache der Blechdicke
Um diese Defekte zu vermeiden, ist es notwendig, den kleinsten Biegeradius zu betrachten. Der kleinste Biegeradius variiert jedoch je nach Material, Blechdicke, Matrize und anderen Faktoren, weshalb es schwierig ist, den korrekten Wert anhand einer mathematischen Formel zu berechnen. Daher ist es erforderlich, den kleinsten Biegeradius auf der Grundlage von Erfahrungen oder Tests festzulegen und Gegenmaßnahmen zur Vermeidung von Rissen in die Konstruktion und die Metallverarbeitung einzubeziehen.
- Setzen Sie die Biegelinie senkrecht zur Walzrichtung.
- Wählen Sie ein Material, das eine hohe Duktilität aufweist.
- Wählen Sie ein Material mit kleinen Kristallkörnern oder reduzieren Sie die Größe der Kristallkörner durch Erhitzen.
- Versetzen Sie die Biegelinie von der Konturlinie des Blechs, um die Wahrscheinlichkeit zu verringern, dass beim Biegen des Blechs durch unzureichende Verlängerung Risse entstehen.
- Wenn ein gestanztes Blech gebogen wird, dehnt sich die gescherte Oberfläche leichter aus, ohne zu reißen, als die gebrochene Oberfläche. Biegen Sie es so, dass die Seite mit der Scherschräge nach außen zeigt.
- Verwenden Sie eine Biegebreite, die mindestens achtmal größer ist als die Blechdicke.
Es ist zwar wichtig, auf das Design und die Materialien zu achten, um Risse und andere Defekte zu vermeiden, aber es ist auch entscheidend, dass das Material innerhalb der Toleranzen in die richtige Form gebogen wird. Im nächsten Abschnitt werden Methoden zur Messung des Biegeradius, die Herausforderungen der jeweiligen Methoden, sowie geeignete Lösungsvorschläge vorgestellt.
Herausforderung bei gängigen Messungen von Biegeradien
Wenn eine höhere Biegegenauigkeit erforderlich ist, wird es schwieriger, Fehler vollständig zu vermeiden, selbst wenn das Material, die Konstruktion und die Presswerkzeuge richtig gewählt sind. Risse, Absplitterungen und fehlerhafte Formen (z. B. ein größerer Biegeradius aufgrund von Rückfederung) können zu Herausforderungen führen, wie z. B. geringere Produktionsquoten, schlechte Qualität und Bruch von Produkten.
Daher ist es sehr wichtig, die Formen von möglichst vielen gebogenen Produkten während der Versuche und bei Änderungen des Materials oder der Biegebedingungen präzise zu messen und zu prüfen. Bei der Messung des Biegeradius werden neben handgeführten Werkzeugen wie Radiusmessgeräten auch 3D-Koordinatenmessgeräte, Profilprojektoren und andere Messgeräte eingesetzt. Es gibt jedoch verschiedene Herausforderungen bei der Messung des Biegeradius mit diesen gängigen Messgeräten.
Herausforderungen bei der Messung von Biegeradien mit einem 3D-Koordinatenmessgerät

Für eine normale Messung eines gebogenen Messobjekts mit einem 3D-Koordinatenmessgerät ist es erforderlich, mit der Spitze des Messtasters mehrere Punkte auf der Oberfläche des Messobjekts zu berühren.
Wenn die Messfläche groß ist, kann die Präzision der Messung verbessert werden, indem die Anzahl der Messpunkte erhöht wird, um mehr Messdaten zu sammeln.
Dies beinhaltet jedoch die folgenden Herausforderungen:
- Die Messung nimmt viel Zeit in Anspruch. Die Messung ist sehr aufwändig, insbesondere bei hochpräzisen Messungen einer großen Fläche, da viele Punkte gemessen werden müssen.
- Wenn ein kleines Messobjekt vertiefte Teile, eine komplexe Form oder einen kleinen Biegeradius hat, kann es für den Messtaster schwierig sein, die Punkte zu berühren.
- Messungen erfordern Geschick und Erfahrung. Nur eine begrenzte Anzahl von Mitarbeitern ist in der Lage, Messungen durchzuführen, was zu ineffizienter Arbeit führt.
- Die tabellarische Erfassung der Messdaten und die Berechnung der Werte erfordert ebenfalls Fachwissen, Erfahrung und viel Zeitaufwand.
Herausforderung bei der Messung des Biegeradius mit einem Profilprojektor

Ein Profilprojektor ist eine Art optisches Messgerät, dessen Messung ähnlich wie die eines optischen Mikroskops funktioniert. Dieses Messgerät strahlt Licht unterhalb des Messobjekts aus und projiziert das Profil auf einen Bildschirm.
Einige große Profilprojektoren haben einen Bildschirm mit einem Durchmesser von mehr als 1 m. Diese Profilprojektoren können ein projiziertes 2D-Profil über eine vergrößerte Zeichnung legen, um Unterschiede zwischen beiden visuell zu erkennen. Dies erfordert jedoch viel Arbeit und Geschick.
Bei der Messung mit einem Profilprojektor treten folgende Herausforderungen auf:
- Bei der Positionierung des Messobjekts ist eine Nivellierung erforderlich. Einige Probenformen können nicht gemessen werden.
- Da gebogene Messobjekte dreidimensionale Formen haben, ist es unmöglich, die Bedingungen der gesamten gebogenen Oberfläche anhand eines 2D-Profils, das von der Seite des Messobjekts projiziert wird, zu bestimmen.
- Die Messmethode variiert bei verschiedenen Anwendern leicht, sodass Abweichungen bei den Messwerten wahrscheinlich sind. Die Unterschiede zwischen den projizierten Abmessungen und der Zeichnung können nicht in numerischer Form ermittelt werden und die Profilform muss auf Pauspapier übertragen werden, was die Speicherung und den Vergleich der Daten erschwert.
Insgesamt ist diese Methode mit vielen Herausforderungen verbunden. Nicht alle Mitarbeiter am Arbeitsplatz können Profile präzise messen und nicht alle Messobjekte können gemessen werden. Außerdem müssen einige Proben aufgrund der Form des Messobjekts zugeschnitten werden.
Lösung von Herausforderungen bei der Messung von Biegeradien
Gängige Messgeräte sind auf die Erfassung von Punkten oder Linien beschränkt oder können nur 2D-Profile vergleichen. Dies führt zu einer geringen Zuverlässigkeit der Messung und macht es schwierig, numerische Werte zu erhalten.
Um diese Messprobleme zu lösen, hat KEYENCE das 3D-Profilometer der Modellreihe VR entwickelt.
Die Modellreihe VR erfasst präzise die 3D-Form der gesamten Oberfläche, ohne das Messobjekt zu berühren. Mit diesem System können Sie präzise und wiederholbare Messungen in nur einer Sekunde durchführen, indem Sie das Messobjekt auf den Objekttisch legen und die Aufnahme per Klick starten. Das System legt den Messbereich und die Bedingungen automatisch fest. Dadurch werden präzise quantitative Messungen gewährleistet, die keine anwenderspezifischen Unterschiede aufweisen. In diesem Abschnitt werden einige Vorteile der Modellreihe VR vorgestellt.
Vorteil 1: Die 3D-Form einer gesamten Oberfläche kann in nur wenigen Sekunden erfasst werden
Die Modellreihe VR erfasst vollständige Oberflächendaten in nur einer Sekunde. Sie ermöglicht eine präzise Messung und Beurteilung der maximalen und minimalen Oberflächenunregelmäßigkeiten über das gesamte gebogene Messobjekt.
Die Modellreihe VR kann Profilmessungen auch an bestimmten Bereichen durchführen. So können nach der Messung Profile an verschiedenen Stellen aus den 3D-Scandaten erfasst werden, ohne das Messobjekt erneut scannen zu müssen.

Vorteil 2: Die intuitive Bedienung sorgt für präzise und wiederholbare Messungen, auch durch ungeübte Anwender
Die Messung von 3D-Formen kann ganz einfach durchgeführt werden, indem Sie das Messobjekt auf den Objekttisch legen und die Aufnahme starten. Da eine automatische Positionskorrektur anhand von Messobjektdaten möglich ist, ist eine Nivellierung oder Positionierung nicht erforderlich. Diese Modellreihe umfasst auch die neue „Smart Measurement“-Funktion, die den Messbereich automatisch konfiguriert und den Objekttisch entsprechend der Größe des Messobjekts bewegt. Damit entfällt die Arbeit, die für die Einstellung der Messlänge und des Z-Bereichs erforderlich ist.

Die große Auswahl an Hilfswerkzeugen ermöglicht eine einfache Einrichtung der gewünschten Messungen.
Zusätzlich zur einfachen Konfiguration ermöglichen die Hilfswerkzeuge eine einfache Bedienung des Systems, sodass selbst ungeübte Anwender Formen präzise messen können. Dadurch kann die Anzahl der Proben nicht nur für Prototypen und Versuche, sondern auch für die Messung und Prüfung von Produkten problemlos erhöht werden.









Zusammenfassung
Die Modellreihe VR kann 3D-Messobjekte präzise und sofort mit hoher Geschwindigkeit messen, ohne das Messobjekt zu berühren. Selbst der Radius eines gebogenen Messobjekts, Oberflächenunregelmäßigkeiten und andere komplexe Messobjekte können in kürzester Zeit gemessen werden. Die Modellreihe VR löst viele Herausforderungen, die bei gängigen Messgeräten auftreten können.
- Mit diesem System können Querschnitte gemessen werden, ohne das Messobjekt zu schneiden.
- Dies verhindert durch menschliche Faktoren bedingte Abweichungen und ermöglicht so eine zuverlässige quantitative Messung.
- Es sind weder Positionierung noch andere Vorbereitungen erforderlich. Anwender können einfach das Messobjekt auf den Objekttisch platzieren und die Aufnahme per Klick starten. Damit muss für die Messung kein Fachpersonal mehr herangezogen werden.
- Da 3D-Formen mit hoher Geschwindigkeit und Präzision gemessen werden können, ist die Messung einer großen Anzahl von Proben in kurzer Zeit möglich. Dies ist nützlich für Qualitätsverbesserungen.
Dieses System ermöglicht auch Vergleiche mit früheren 3D-Messdaten und CAD-Daten sowie eine einfache Datenanalyse, wie z. B. die Verteilung innerhalb der Toleranzen. Es kann effektiv für eine Vielzahl von Zwecken eingesetzt werden, einschließlich Produktentwicklung, Trendanalysen in der Produktion und Stichprobenprüfungen.