Was ist IoT / Industrie 4.0?
Iot ist eine Abkürzung für „Internet of Things“ (Internet der Dinge). Zum besseren Verständnis sollten Sie sich eine Umgebung vorstellen, in der Dinge, die über Kommunikationsfunktionen verfügen, über das Internet miteinander verbunden sind.
Diese „Dinge“ können Industrieanlagen, Autos und Haushaltsgeräte sein. Diese Seite gibt einen Einblick darüber, wie IoT in der Betriebsautomatisierung eingesetzt werden kann.
Verbindung von Betriebsanlagen über IoT
Die Anbindung Ihrer Betriebsanlagen an ein Netzwerk bringt einige Vorteile mit sich:
- Aufrechterhaltung der Kontrolle durch Überwachung und Sammlung von Daten aus der Anlage.
- Wertschöpfung durch die Analyse gespeicherter Daten.
Die Nutzung des Iot in Betriebsanlagen beginnt mit dem Anschluss Ihrer Sensoren und Geräte an ein Netzwerk und dem Sammeln dieser Daten. Das IoT kann die Produktivität in der Fertigungsindustrie erheblich verbessern, indem es den Produktionsbetrieb in Verbindung mit einem ERP-System rationalisiert oder die physische Distribution durch die Anbindung an andere Betriebsanlagen optimiert.
Unternehmensressourcenplanung einschließlich Finanz- und Rechnungswesen
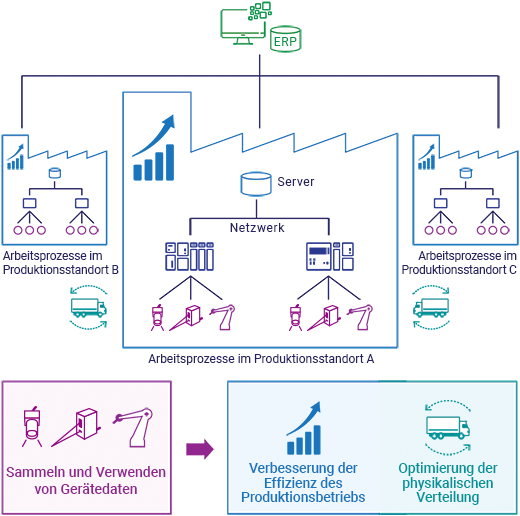
Industrie 4.0 - die Revolution in der Fertigungsindustrie
Der Begriff leitet sich aus einem Projekt der deutschen Bundesregierung ab. Mit der "Hightech-Strategie 2025" soll die Innovationskraft gefördert werden, um die wirtschaftliche Position Deutschlands zu stärken.
Was ist Industrie 4.0?
Industrie 4.0 bezeichnet die Digitalisierung von industriellen Produktionsprozessen mit dem Ziel, die Prozesse effizienter zu gestalten. Im Kern soll dies durch die Vernetzung aller im Prozess beteiligter Systeme erfolgen, sprich jeder Sensor in einer Betriebsanlage ist miteinander vernetzt und wiederum alle Betriebsanlagen sind über digitale Systeme verbunden.
Industrie 4.0 wird auch als vierte industrielle Revolution bezeichnet, deren Ziel es ist, die Produktivität in der gesamten Fertigungsindustrie zu verbessern.
<Geschichte der industriellen Revolutionen >
Die Mechanisierung der Produktionsfabriken durch Wasserkraft- und Dampfmaschinen, die Ende des 18. Jahrhunderts begann, wird als die erste industrielle Revolution bezeichnet. Die Serienproduktion, die durch die Nutzung von Strom im frühen 20. Jahrhundert möglich wurde, wird als zweite industrielle Revolution bezeichnet. Die Digitalisierung mit Elektronik- und IT-Technologien im späten 20. Jahrhundert wird als dritte industrielle Revolution bezeichnet.
Industrie 4.0 ist ein nationales Projekt der Bundesregierung, das sich als „industrielle Revolution der nächsten Generation“ positioniert. Sie wird seit Mitte der 2000er-Jahre durch die Zusammenarbeit zwischen Industrie, Regierung und Hochschulen gefördert und ist in der Erwartung definiert, die vierte industrielle Revolution zu sein.
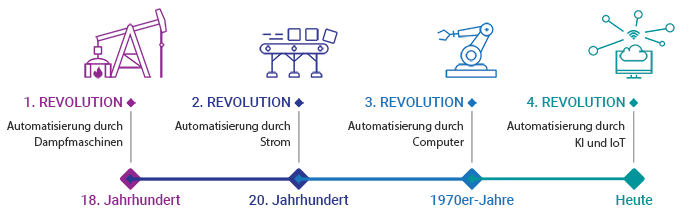
Technologien zur Materialisierung der Industrie 4.0
Industrie 4.0 erfordert zweierlei Arten von innovativen Technologien.
Der erste Typ sind Infrastrukturtechnologien für die Kommunikation, Speicherung und Verarbeitung der enormen Datenmengen, die sich aus der Verbindung aller Bereiche ergeben. Ein Beispiel für solche Technologien ist das Fog Computing.
Bisher wurde Cloud Computing für die Datenkommunikation und -verarbeitung eingesetzt. Die Materialisierung von Industrie 4.0 erfordert die Fähigkeit, weitaus mehr Daten zu verarbeiten. Wenn Cloud Computing zur Verarbeitung all dieser Daten eingesetzt wird, kann sich der Netzwerkverkehr auf eine außergewöhnliche Größe ausdehnen und über das kontrollierbare Maß hinausgehen.
Als Gegenmaßnahme wird zwischen der Cloud und den Geräten eine verteilte Verarbeitungsumgebung namens Fog implementiert, um dieses enorme Datenvolumen im Voraus zu verarbeiten und Überkonzentrationen in der Cloud zu vermeiden. Dieser Ansatz der Verwendung von verteilter Verarbeitung zur Verhinderung der Lastkonzentration des Netzwerkverkehrs ist das Konzept des Fog Computing.
Ein weiteres Mittel sind KI-Technologien (Künstliche Intelligenz). Der Aufbau der notwendigen Infrastruktur und das Sammeln enormer Datenmenge bringt nur einen Mehrwert, wenn wir diese auch nutzen können.
Hierbei kommen die KI-Technologien ins Spiel. Von der KI wird erwartet, dass sie eine Vielzahl von Aufgaben erfüllt - von der Unterstützung bei Plänen und Entscheidungen bis hin zur Bereitstellung optimaler Vorhersagen, die für den Menschen schwierig zu treffen sind.
Vorteile für Fertigungslinien
Die Materialisierung von Industrie 4.0 wird zu reduzierten Produktionskosten und deutlich kürzeren Durchlaufzeiten führen.
Denn die Materialisierung fördert die Einführung digitaler Daten in Produktionsprozesse sowie deren Automatisierung und virtuellen Betrieb, was eine höhere Integration der Engineering-Kette und der Lieferkette ermöglicht.
So erlauben es beispielsweise präzise KI-basierte Simulationen der Bedarfs- oder der Einführungsplanung den Entwicklungs- oder Konstruktionsmitarbeitern, diverse Prozesse zu verkürzen oder zu überspringen.
Darüber hinaus verhindert die rechtzeitige Synchronisation von Stücklisten zwischen Konstruktionsbüro und Produktionsstätte, dass Fertigungsprozesse umgekehrt oder fehlerhafte Ziele erzeugt werden. Wenn die Daten zwischen Herstellern und Materiallieferanten synchronisiert werden können, können Materialien automatisch und zum besten Zeitpunkt bereitgestellt werden.
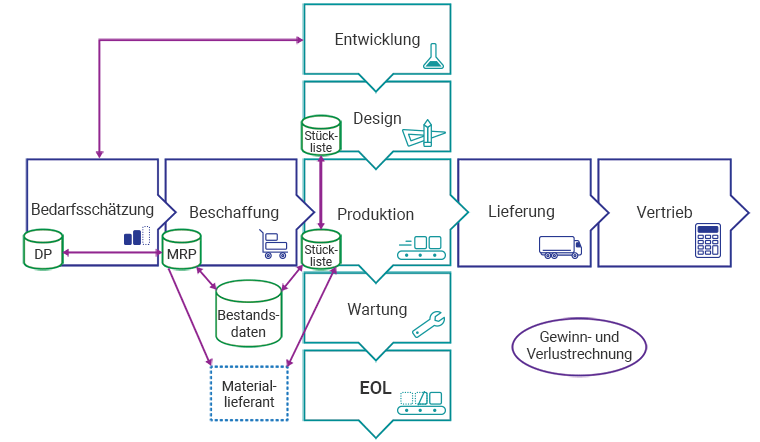
Datensynchronisation/-austausch
Engineering-Kette: der Prozess von der Produktentwicklung und dem Design bis zur Einstellung der Produktion
Lieferkette: der Prozess von der Bedarfsschätzung und Materialbeschaffung eines Produkts bis zur Lieferung an den Verbraucher
Smart Factories als Ziel von Industrie 4.0
Eine Smart Factory ist eine Betriebsanlage, in der Industrie 4.0 realisiert wurde. Es handelt sich um eine Produktionsstätte, an der alle Geräte, Roboter und Sensoren in der Betriebsanlage an ein Netzwerk angeschlossen sind, um verschiedene Arten von Informationen zu visualisieren und die kausalen Zusammenhänge zwischen diesen Informationen zu klären.
Die Realisierung des Smart-Factory-Konzepts führt zu Produktivitätssteigerungen und Kostensenkungen. Die Informationen werden in Echtzeit gesammelt, was eine entsprechende Programmierung von Anlagen und Robotern erfordert. Die Arbeitseffizienz verbessert sich und Probleme, die durch menschliches Versagen verursacht werden, können verhindert werden.

Sensoren für die Industrie 4.0
Sensoren sind für die Funktion von Smart Factories unerlässlich. Diese haben die Eigenschaft, die Erfassung und Sammlung verschiedener Daten und das Abrufen oder Verfolgen von Fertigungsbedingungen oder Chargeninformationen von Produkten zu ermöglichen.
Wenn KI-Technologien mit Sensoren kombiniert werden, trifft die KI Entscheidungen autonom und arbeitet mit Maschinen und Robotern zusammen, um die Produktion zu optimieren.
Dieser Prozess hebt sich deutlich von der einfachen Automatisierung ab und unterscheidet sich auch stark von den Fertigungslinien, die auf digitalen Daten der dritten industriellen Revolution basieren.
KEYENCE-Lösungen für Probleme mit Sensoren
Voraussetzung für Industrie 4.0 ist der Datenaustausch von Geräten auf verschiedenen Ebenen.
Das Informationssystem in einer Betriebsanlage kann wie folgt als eine Struktur von Schichten dargestellt werden:
- ERP-System (Enterprise Resource Planning) zur Verwaltung von Betriebsmitteln wie Finanz- und Rechnungswesen
- MES (Manufacturing Execution System) zur Bedienung und Steuerung von Produktionslinien
- Industrielles Steuerungssystem zur computergestützten Systemüberwachung und Prozesssteuerung
- Steuerung/SPS (Speicherprogrammierbare Steuerung)
- Industrieroboter, Sensoren und Aktoren am Standort
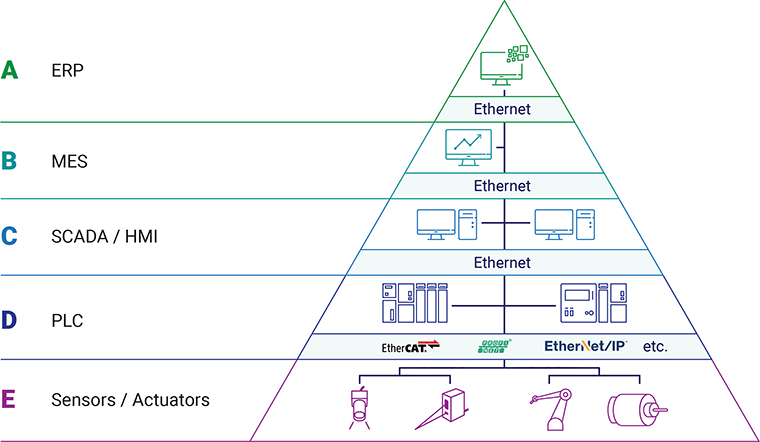
Wenn Sensoren oder andere Endgeräte an ein Netzwerk angeschlossen werden, treten aufgrund der Verwendung vieler verschiedener Standards häufig Probleme auf. Da sich die Einführung von IoT in einer Übergangsphase befindet, bauen Unternehmen Netzwerke mit unterschiedlichen Kommunikationsstandards auf, was die Verbindung zwischen den Netzwerken oft erschwert. Dadurch wird auch der Anschluss von Sensoren und anderen Geräten verhindert, die nicht mit der entsprechenden Norm kompatibel sind.
Im derzeitigen Übergangszustand, in dem jeder Bestandteil einer Betriebsanlage durch Industrie 4.0 vernetzt wird, unterstützt KEYENCE Kunden vor Ort durch die Entwicklung von Produktionslinien, die mit verschiedenen Netzwerken kompatibel sind und sich an Veränderungen anpassen können.