Maßhaltigkeitsprüfung von Vakuumkammern
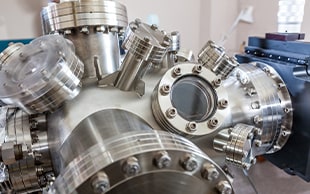
Mit der Verbreitung des Technologiestandards der fünften Generation (5G) und der digitalisierten Automobilausrüstung soll die Nachfrage nach Halbleitern in einen Superzyklus* eingetreten sein. Die Hersteller von Halbleitern müssen dringend neue Technologien entwickeln und die Produktivität verbessern, um der wachsenden Nachfrage und der höheren Funktionalität gerecht zu werden. Die Leistung von Vakuumkammern, die in vielen Halbleiterherstellungsprozessen verwendet werden, ist ein besonders wichtiges Element für die sich ständig weiterentwickelnden Halbleiterherstellungstechnologien.
In diesem Abschnitt werden grundlegende Kenntnisse vermittelt, wie z. B. die Anwendung von Vakuumkammern in der Halbleiterfertigung, ihr Aufbau, Probleme bei der Form- und Maßhaltigkeitsprüfungen, die ihre Leistung bestimmen, und Lösungen für diese Probleme.
* Ein Preisanstieg, der in einer konstanten Häufigkeit auftritt, eine Art periodischer Marktpreisschwankung und Konjunkturzyklus.
- Was ist eine Vakuumkammer?
- Anwendungen von Vakuumkammern in der Halbleiterfertigung
- Aufbau der Vakuumkammer
- Notwendigkeit der Maßhaltigkeitsprüfung von Vakuumkammern
- Maßhaltigkeitsprüfung von Vakuumkammern
- Probleme der Maßhaltigkeitsprüfung von Vakuumkammern und ihre Lösungen
- Optimierung der Maßhaltigkeitsprüfung von Vakuumkammern
Was ist eine Vakuumkammer?

Eine Vakuumkammer ist ein Behälter, der einen Unterdruck erzeugt. Unterdruck ist ein Zustand, in dem der Druck niedriger ist als der Atmosphärendruck. Vakuumpumpen werden an eine Vakuumkammer angeschlossen, um Luft aus der Vakuumkammer anzusaugen und darin einen Unterdruck zu erzeugen.
Das Plasma, das für viele Geräte zur Halbleiterherstellung benötigt wird, wird im Vakuum erzeugt. Ein Vakuum enthält weniger Verunreinigungen und senkt den Siedepunkt, sodass sich dünne Schichten der gewünschten Materialien abscheiden oder sie sieden lassen. Dank dieser Eigenschaften werden Vakuumkammern in vielen Halbleiterherstellungsprozessen wie Belichtung, Beschichtung, Ätzen und Sputtern eingesetzt.
Anwendungen von Vakuumkammern in der Halbleiterfertigung
Vakuumkammern werden für viele Geräte in der Halbleiterfertigung verwendet. Einige typische Geräte werden in diesem Abschnitt vorgestellt.
Gerät für die chemische Gasphasenabscheidung (CVD)
Eine CVD-Anlage wird zur Herstellung dünner Schichten verwendet. Mit einer CVD-Anlage können ca. 10 bis 1000 nm dicke Schichten auf Silizium-Wafern abgeschieden werden, darunter Schichten, die Halbleiter vor Wasser und Staub schützen, Verdrahtungsschichten und Isolierschichten. Dünne Schichten werden durch chemische Reaktionen von Gasen erzeugt, die durch Hitze, Licht oder Plasma ausgelöst werden.
CVD-Geräte, die Plasma verwenden, produzieren dünne Schichten in Vakuumkammern. Mit der Plasmamethode können dünne Schichten bei niedrigeren Temperaturen als mit Wärme oder Licht hergestellt werden. Mit ihr können auch dünne Filme auf schmalen Rillen hergestellt werden, was den Einsatz in vielen Halbleiterherstellungsprozessen ermöglicht.
Ätzgerät
Ein Ätzgerät dient zur feinen Bearbeitung von Halbleiteroberflächen, z. B. durch tiefe Rillengravur mit Breiten von etwa 100 bis 1000 nm. Es gibt zwei Arten von Ätzgeräten: Nassätzgeräte und Trockenätzgeräte. Ein Nassätzgerät entfernt eine dünne Schicht mit Hilfe einer chemischen Reaktion in einer Lösung aus Säure, Lauge oder anderen Substanzen und entfernt die freiliegenden Bereiche weiter. Ein Trockenätzgerät verwendet Plasma im Hochvakuum. Bei dieser Methode wird mit Hilfe von Gasen in einer Vakuumkammer ein Plasma erzeugt und durch eine chemische Reaktion und den Beschuss mit beschleunigten Ionen ein dünner Film entfernt.
Im Vergleich zu Nassätzgeräten können Trockenätzgeräte, die Plasma verwenden, feinere Bearbeitungen durchführen und bieten eine bessere Äolotropie. Darüber hinaus verwenden einige kürzlich entwickelte Trockenätzgeräte ein hochdichtes Plasma, das den Durchsatz auch bei Wafern mit großem Durchmesser aufrechterhalten kann.
Sputtering-Gerät
Ein Sputtering-Gerät erzeugt dünne Schichten im Vakuum.
Dieses Gerät erzeugt ein Argon-Plasma in einer Vakuumkammer. In der Kammer lässt das Sputtering-Gerät Argon-Ionen auf einen Block, dem so genannten Messobjekt, treffen, um Metallatome auszustoßen und auf Wafern abzuscheiden.
Sputtering-Geräte können dünne Schichten von Metallen abscheiden, die mit CVD-Geräten und Vakuumabscheidungsmethoden nur schwer zu trennen sind, wie z. B. Metalle mit hohem Schmelzpunkt und Legierungen. Gleichzeitig muss das Vakuumniveau in einer Vakuumkammer etwa in zweistelligem Bereich höher liegen als bei CVD-Geräten, was ein hocheffektives Vakuumsystem erfordert.
Belichtungsgerät für sehr ultraviolette Lithographie* (EUV)
EUV-Belichtungsgeräte sind die neuesten Belichtungsgeräte, die eine weiche Röntgenstrahlung als Lichtquelle verwenden. Die in dieser Technologie verwendete weiche Röntgenstrahlung hat eine Wellenlänge von 13,5 nm, etwa ein Zehntel oder weniger als eine übliche ArF-Lichtquelle. Durch die Verwendung von Licht mit einer sehr kurzen Wellenlänge können Schaltkreismuster mit einer Feinheit von 5 nm und 3 nm auf Wafer übertragen werden, was mit üblichen Technologien schwierig war.
Die weiche Röntgenstrahlung, die in EUV-Belichtungsgeräten verwendet wird, wird in einer Vakuumkammer emittiert. Das optische System einschließlich des Bestrahlungsspiegels befindet sich ebenfalls in dieser Kammer. Weiche Röntgenstrahlen werden in der Luft absorbiert. Dies erfordert ein hohes Vakuumniveau und das Entfernen von Wasser in der Kammer.
Obwohl EUV-Belichtungsgeräte noch nicht weit verbreitet sind, wird erwartet, dass sie sich zur führenden Belichtungsausrüstung entwickeln werden, und die Halbleiterhersteller heftig um ihre Installation konkurrieren werden. EUV-Belichtungsgeräte, die ursprünglich für die Herstellung von Logik-Halbleitern eingeführt wurden, kommen auch bei dynamischen Direktzugriffsspeichern (DRAMs) zum Einsatz, die deutlich kleiner und viel schneller werden sowie eine viel höhere Kapazität aufweisen. Es wird erwartet, dass sich EUV-Belichtungsgeräte in diesem Bereich weiter verbreiten werden.
*Sehr ultraviolett
Aufbau der Vakuumkammer
Vakuumkammern erzeugen einen Unterdruck, indem sie den Druck mit Hilfe einer Vorvakuumpumpe und einer Vakuumpumpe (Hauptpumpe) absenken. Typische Vakuumkammern werden aus rostfreiem Stahl oder mit Nickel beschichtetem Baustahl hergestellt, während Ultrahochvakuum-Systeme aus Aluminiumlegierungen gefertigt werden.
Die Wafer werden in eine Vakuumkammer eingeführt und in der Kammer bearbeitet, z. B. durch Beschichten und Ätzen. Für eine qualitativ hochwertige Verarbeitung mit minimalen Verunreinigungen und hoher Haftung muss die Vakuumkammer ein hohes Vakuum erreichen, um Verunreinigungen in der Luft so weit wie möglich zu minimieren. Einige ihrer Teile, wie z.B. Flansche, die zur Montage von Komponenten von Vakuumkammern verwendet werden, müssen mit hoher Genauigkeit bearbeitet werden.

- A
- Vakuumkammer
- B
- Vakuumpumpe (Hauptpumpe)
- C
- Wafer
- D
- Vorvakuumpumpe
Notwendigkeit der Maßhaltigkeitsprüfung von Vakuumkammern
Die Leistung von Halbleiterbauelementen steht in direktem Zusammenhang mit dem Vakuumniveau in einer Vakuumkammer. Abnormale Vakuumniveaus haben negative Auswirkungen auf physikalische und chemische Prozesse wie elektrische Entladungen, Ionisierung und Sputtern, insbesondere in Geräten, die Plasma erzeugen.
Eine der Hauptursachen für negative Einflüsse ist ein Phänomen namens Luftleck. Bei diesem Phänomen dringt Luft durch Lücken an den Stirnseiten oder Dichtungsflächen der Kammer in eine Vakuumkammer ein. Wenn Luft in eine Vakuumkammer eindringt, sinkt das Vakuumniveau. Dadurch werden die chemischen Reaktionen, die für Beschichten, Ätzen, Sputtern und andere Prozesse erforderlich sind, gestört, was zu Verarbeitungsfehlern führt.
Gase können auch aufgrund von Verbindungsfehlern von Verbindungsstücken oder geschweißten Abschnitten oder aufgrund von Installationsfehlern von Verpackungsmaterialien oder anderen Teilen austreten und zu Gasvergiftungen, Bränden oder Explosionen führen.
Luft- und Gaslecks können durch sorgfältige Maßnahmen verhindert werden, wie z. B. das Sicherstellen der Ebenheit der Endflächen und Dichtungsflächen von Vakuumkammern, das Prüfen der Luftdichtheit von Gasflusssystemen, einschließlich des Zustands der Flanschmontage, und das Spülen dieser Gasflusssysteme mit Inertgasen. Das Wichtigste ist jedoch, dass ihre Formen und Abmessungen bei der Herstellung genau gemessen werden.
Maßhaltigkeitsprüfung von Vakuumkammern
Vakuumkammern werden aus rostfreiem Stahl, vernickeltem Baustahl und Aluminiumlegierungen durch Verbinden von Blechen (in der Regel durch Schweißen), spanende Bearbeiten von Blöcken oder Schmieden hergestellt. Wenn eine Vakuumkammer durch Schweißen verbunden wird, muss sie auf schweißbedingte Verformungen geprüft werden, und wenn eine Vakuumkammer durch spanende Bearbeitung oder eine Kombination aus Schmieden und maschinellem Bearbeiten hergestellt wird, auf Verformungen, die durch Schneiddruck oder andere Faktoren verursacht werden.
Maßhaltigkeitsprüfungspunkte
Es gibt viele zu messende Punkte. In diesem Abschnitt werden die Ebenheit der Stirn- und Dichtflächen einer Vakuumkammer, für die Form- und Maßgenauigkeit besonders wichtig sind, die Montagegenauigkeit von Absperrschiebern (Vakuumventilen) und Vorsichtsmaßnahmen für diese Messungen vorgestellt.
Ebenheit der Stirnseiten und Dichtflächen
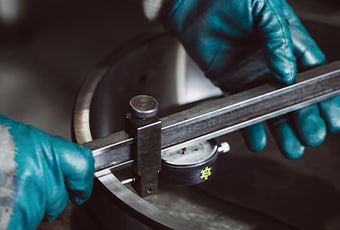
Die Ebenheit der Stirnseiten und Dichtflächen von Öffnungen und Verbindungen mit Deckeln einer Vakuumkammer muss gemessen werden.
Die Seitenlänge von großen rechteckigen Vakuumkammern oder der Durchmesser von großen zylindrischen Vakuumkammern kann 1 m überschreiten. Selbst subtile Fehler können eine ordnungsgemäße Verbindung verhindern und Probleme wie Leckagen verursachen. Fehler in der Ebenheit beeinträchtigen auch die Betriebsgenauigkeit von Vakuumkammern nach der Installation.
Eine sorgfältige Inspektion ist erforderlich, einschließlich der Messung der Bearbeitungsgenauigkeit in jedem Fertigungsprozess und der Überprüfung anhand der CAD-Designdaten.
Montagegenauigkeit von Absperrschiebern (Vakuumventilen)
Ein Absperrschieber trennt ein Vakuum von einem anderen Vakuum oder ein Vakuum von der Umgebungsluft. In Geräten zur Halbleiterverarbeitung werden Absperrschieber zwischen der Vakuumkammer und den Vakuumpumpen installiert, um den Druck in der Vakuumkammer zu regulieren.
Absperrschieber trennen ein Vakuum von der Umgebungsluft und halten dabei das Vakuum aufrecht. Daher wirkt sich ihre Montagegenauigkeit direkt auf die Luftdichtheit von Vakuumkammern aus. Eine niedrige Montagegenauigkeit kann dazu führen, dass die Dichtungen nicht funktionieren und während des Betriebs, Luft- oder Gaslecks in den Vakuumkammern entstehen.
Die Montagegenauigkeit von Absperrschiebern, wie z. B. Winkel und Positionen, muss streng gemessen werden.


Probleme der Maßhaltigkeitsprüfung von Vakuumkammern und ihre Lösungen
Es ist wichtig, die Form und die Abmessungen jedes Teils vor der Montage und der montierten Vakuumkammern zu messen. Für diese Messungen sind in der Regel dreidimensionale Kontrollelemente und eine Genauigkeit in der Größenordnung von Mikrometern erforderlich, sodass die Leistungsfähigkeit von Handmessmitteln wie Maßbändern und Messschiebern in diesen Situationen begrenzt ist. Daher werden häufig Portal-Koordinatenmessgeräte (KMG) für diese Messungen verwendet.
Es ist jedoch sehr aufwändig, große Vakuumkammern von der Produktionsstätte in einen Messraum zu transportieren und dort auf ein 3D-Koordinatenmessgerät (KMG) zu setzen. Diese Methode birgt auch das Problem, dass keine zeitnahe Messung möglich ist, wenn eine Messung vor Ort erforderlich ist. Ein weiteres Problem ist, dass für die Messung von großen Kammern mit einer Größe von über 1 m ein hohes Maß an Messkenntnissen und zwei oder drei Personen erforderlich sind.


Um diese Probleme zu lösen, werden in immer mehr Fällen die neuesten 3D-Koordinatenmessgeräte (KMG) eingesetzt. Das Mobile 3D-Koordinatenmessgerät der Modellreihe WM von KEYENCE ermöglicht eine hochpräzise Maßhaltigkeitsprüfung von großen Vakuumkammern durch eine einzige Person mit dem kabellosen Messtaster. Selbst vertiefte Bereiche von Messobjekten können ohne Bewegungseinschränkungen innerhalb des Messbereichs erreicht werden, was die Messung durch einfaches Antasten des Messobjekts mit dem kabellosen Messtaster ermöglicht. Darüber hinaus ist die Modellreihe WM tragbar und ermöglicht Messungen an beliebigen Punkten zu beliebigen Zeitpunkten, sei es in der Fertigung oder auf der Baustelle. Im Gegensatz zu Messungen mit Handmessmitteln variieren die gemessenen Werte nicht, was eine quantitative Messung ermöglicht.
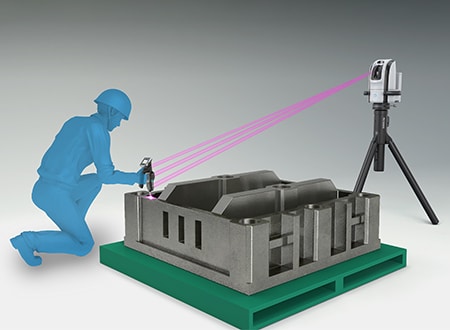
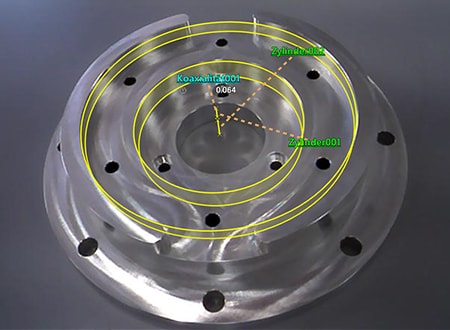
Messung der Ebenheit von Stirnseiten und Dichtflächen
Große Vakuumkammern sind etwa 5 m lang, 3 m breit und wiegen etwa 4 Tonnen. Selbst bei großen Vakuumkammern ist in vielen Fällen eine hohe Messgenauigkeit erforderlich. Um die Ebenheit und die Abmessungen der einzelnen Teile genau zu messen, ist ein Portal-Koordinatenmessgerät (KMG) erforderlich. Für die Messung einer großen Vakuumkammer mit einem Portal-Koordinatenmessgerät muss jedoch die Kammer aus der Werkzeugmaschine mühsam entfernt und in den Messraum gebracht werden.
Messungen an Werkzeugmaschinen, die mit Handmessmitteln durchgeführt werden, werfen ebenfalls viele Probleme auf. Es ist beispielsweise nicht möglich, mit diesen Werkzeugen 3D-Maße zu messen. Messungen nehmen zudem Zeit in Anspruch, wodurch die Arbeitsgeschwindigkeit von Werkzeugmaschinen sinkt. Wenn Vakuumkammern bei der Überprüfung der endgültigen Genauigkeit feinjustiert werden, ist es außerdem besser, ihre Abmessungen auf Werkzeugmaschinen zu messen, anstatt sie auszubauen. Daher ist für die Maßhaltigkeitsprüfung von großen Vakuumkammern ein Koordinatenmessgerät ideal, das kompakt und tragbar ist und die große Fläche eines Vakuumwechslers auf einer Werkzeugmaschine messen kann.
Mit der Modellreihe WM können sogar große Vakuumkammern an Werkzeugmaschinen gemessen werden, ohne dass diese ausgebaut werden müssen. Es ermöglicht die einfache Messung verschiedener Elemente von bearbeiteten Kammern, wie z. B. diagonale Abmessungen, Ebenheit und Rundheit, durch eine einzelne Person. Dies führt zu einer effizienteren Feineinstellung der Bearbeitungsgenauigkeit während der Fertigung und gewährleistet die endgültigen Abmessungen.




Messung der Montagegenauigkeit von Absperrschiebern
Die Genauigkeit des Montagewinkels und der Position von Schiebern, die in einer großen Vakuumkammer montiert sind, wird anhand der Vakuumkammer gemessen. Der Messabstand beträgt mehrere Meter, daher werden ihre Positionen mit Maßbändern oder Messschiebern gemessen und ihre Winkel mit Wasserwaagen oder ähnlichen Messinstrumenten ermittelt. Die mit diesen Handmessmitteln erzielten Messwerte variieren jedoch je nach Winkel und Stärke, mit denen diese Werkzeuge auf das Messobjekt aufgebracht werden, was Schwankungen der Messwerte der verschiedenen Anwender unvermeidbar macht.
Mit der Modellreihe WM ist es möglich, dass eine einzelne Person quantitative Messungen durch einfaches Antasten der Messpunkte mit dem Messtaster durchführen kann. Durch einfaches Berühren des Messobjekts mit dem Messtaster kann der Anwender nicht nur die durch das Schweißen verursachte Verformung und Dehnung, sondern auch den Einbauwinkel der Absperrschieber messen. Es können sogar 3D-Positionskoordinaten gemessen werden. Abweichungen von den geplanten Toleranzen können ebenfalls sofort beurteilt werden.

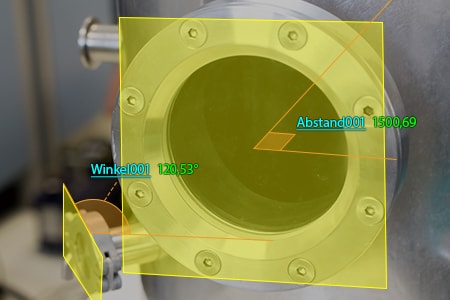
Optimierung der Maßhaltigkeitsprüfung von Vakuumkammern
Die Modellreihe WM ermöglicht die Messung von Formen und Abmessungen der Teile großer Vakuumkammern durch einfache Berührung der mit dem kabellosen Messtaster durch eine einzige Person. Zusätzlich zu den oben vorgestellten Leistungsmerkmalen bietet die Modellreihe WM folgende Vorteile:
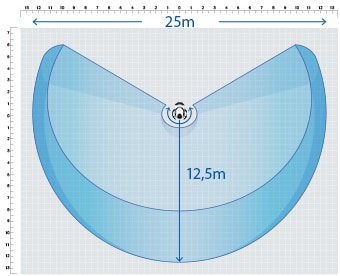
- Hochpräzise Messung über einen großen Bereich
- Ein großer Messbereich bis zu 25 m kann mit hoher Genauigkeit gemessen werden. Die Modellreihe WM ist mit dem Navigationsmessmodus ausgestattet, der die Messung am selben Punkt nach einem gespeicherten Messverfahren ermöglicht, sodass jeder die gleichen Messdaten erhalten kann.

- Messergebnisse können als 3D-Modelle ausgegeben werden.
- Gemessene Elemente können als STEP/IGES-Datei exportiert werden. 3D-CAD-Daten können auf der Grundlage der Messergebnisse eines tatsächlichen Produkts erstellt werden, auch wenn keine Zeichnung vorhanden ist.

- Prüfberichte können mit Fotos erstellt werden
- Prüfberichte können automatisch mit Fotos erstellt werden, die die Erfassung der Messpunkte auf einen Blick ermöglichen. Mit diesen Prüfberichten können Sie nicht nur das Vertrauen Ihrer Geschäftspartner gewinnen, sondern auch Messergebnisse als digitale Daten speichern, was zu einer höheren Effizienz der internen Datenverwaltung führt.
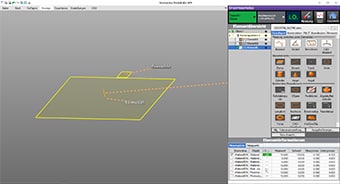
- Leicht verständliche Schnittstelle
- 3D-Koordinatenmessgeräte arbeiten oft mit komplizierten und ungewohnten Befehlen. Die Modellreihe WM bietet eine intuitive Bedienung mit Bildern und Symbolen, wodurch das System leicht bedient werden kann.
Die Modellreihe WM unterstützt in hohem Maße die Analyse, wie z. B. den Vergleich mit 3D-CAD-Daten, sowie die Messung der Abmessungen und Formen der Teile von Vakuumkammern. Sie verbessert die Effizienz der Herstellung von Vakuumkammern und der für ihre Installation und das Qualitätsmanagement erforderlichen Arbeiten erheblich.