Dickenmessung von gezogenen Produkten

Ziehen ist eine Methode des Pressformens, die zur Herstellung von Produkten wie Metallbechern, Behältern und Küchenspülen verwendet wird. Es gilt als das schwierigste Pressverfahren. Während der Umformung entstehen durch Spannung, Reibung und anderen Faktoren leicht Fehler wie ungleichmäßige Dicken und Risse. Aus diesem Grund ist es unerlässlich, nach der Umformung eine Dickenmessung der Produkte durchzuführen und auf Fehler wie Risse und Falten zu prüfen.
In diesem Abschnitt werden typische Ziehverfahren und Arten von Ziehfehlern erklärt, die bei gezogenen Produkten auftreten. Außerdem werden passende Gegenmaßnahmen vorgestellt.
- Ziehen
- Methoden der Druckanwendung bei Ziehmaschinen
- Arten von Ziehverfahren
- Ziehfehler
- Herausforderungen bei gängigen Dickenmessungen von gezogenen Produkten
- Herausforderungen bei der Dickenmessung
- Zusammenfassung: Effizientere Dickenmessung von gezogenen Produkten
Ziehen
Ziehen ist eine Methode des Pressformens, bei der ein Blechzuschnitt zu einem nahtlosen Behälter mit einem Boden geformt wird.
Beim Ziehen wird ein Blechzuschnitt in die Form eines Bechers oder Behälters gebracht, indem der sogenannte Stempel in den Zuschnitt gedrückt wird, der zwischen Matrize und Blechhalter gehalten wird. Ein Ziehverfahren, bei dem die Presstiefe den Stempelradius übersteigt, wird als Tiefziehen bezeichnet. Wenn ein Blechzuschnitt aufgrund seines Materials, seiner Dicke oder anderer Faktoren nicht mit einer einzigen Presse geformt werden kann, kann er schrittweise in mehreren Pressen geformt werden.
Ein Vorteil des Ziehens besteht darin, dass komplex geformte Produkte mit weniger Arbeitsschritten hergestellt werden können als beim Schneiden und Schmieden, bei denen überflüssige Teile weggeschnitten oder gehämmert werden müssen.

- A
- Stempel
- B
- Blechhalter
- C
- Blechzuschnitt
- D
- Matrize
Methoden der Druckanwendung bei Ziehmaschinen
Ziehmaschinen werden grob in zwei Typen eingeteilt: mechanische Pressen und hydraulische Pressen. Mechanische Pressen übertragen die Rotationskraft eines Motors auf den Stempel, um Druck auszuüben. Hydraulische Pressen verwenden hydraulischen Druck, um den Stempel zu verschieben und so Druck auszuüben.
Mechanische Pressen zeichnen sich durch hohe Umformgeschwindigkeiten und gute Wartungsfreundlichkeit aus. Allerdings können sie den Stempel nur in einem begrenzten Bereich bewegen, und eine Druckanpassung ist nicht möglich, weshalb sie für das Tiefziehen ungeeignet sind. Hydraulische Pressen hingegen können die Stärke des ausgeübten Drucks regulieren und verfügen im Vergleich zu mechanischen Pressen über einen längeren Stempelhub und eine einfachere Einstellung der Umformgeschwindigkeit. Hydraulische Pressen erzeugen auch keine Überlast. Sie müssen jedoch regelmäßig gewartet werden, um den Hydraulikdruck einzustellen und das Auslaufen von Hydraulikflüssigkeit zu verhindern.
Das Ziehen erfolgt meist mit mechanischen Pressen – für das Ziehen, das mit mechanischen Pressen nicht möglich ist, werden hydraulische Pressen verwendet. In den letzten Jahren wurden Pressen entwickelt, die eine hochpräzise Druckeinstellung ermöglichen und mit Servomotoren ausgestattet sind, die die Stempelbewegung nicht begrenzen.
Arten von Ziehverfahren
Zu den verschiedenen Arten des Ziehens gehören das Ziehen von zylindrischen, quadratischen und unregelmäßigen Formen sowie eine Art des Ziehens für komplexere Formen. In diesem Abschnitt werden drei gängige Arten vorgestellt.
Ziehen zylindrischer Formen
Bei dieser Methode wird ein Blechzuschnitt in eine zylindrische Form gezogen. Dies ist die einfachste Art des Ziehens, die verwendet wird, um Produkte in Formen wie Tassen und Schalen zu erstellen.

Ziehen quadratischer Formen
Bei dieser Methode wird ein Blechzuschnitt in eine quadratische Rohrform gezogen. Sie wird für die Herstellung von Produkten in Form von quadratischen Behältern und Kisten verwendet. Die Ecken der gezogenen Produkte sind anfällig für Risse und Faltenbildung.

Ziehen unregelmäßiger Formen
Diese Methode wird verwendet, um komplexe Formen zu bilden. Hiermit können andere Formen als Zylinder oder Vierkantrohre gezogen werden, die z. B. zu Kraftstofftanks und Abdeckungen sowie Rippen, die die Oberflächenfestigkeit erhöhen, werden.

Ziehfehler
In diesem Abschnitt werden die Arten und Eigenschaften von Fehlern, die beim Ziehen auftreten, erklärt. Beim Ziehen treten viele Arten von Fehlern auf. Dieser Abschnitt konzentriert sich auf die nachfolgenden gängigen Fehler.

- A
- Rissbildung
- B
- Flanschfalte
- C
- Falte, Schocklinie
- D
- Fresser
- E
- Rückfederung
Rissbildung
Gezogene Blechzuschnitte härten aus und werden spröde. In den spröden Abschnitten treten Eigenspannungen und ein Ungleichgewicht von Zug- und Druckkräften auf, was zu Rissen führt.
- Wandbruch:
- Dabei handelt es sich um einen Riss, der an Wänden auftritt. Wände in Ecken können reißen oder brechen, wenn das Tiefziehen mit dünnem Blech durchgeführt wird.
- Abfallender Boden:
- Die Spannung konzentriert sich an den abgerundeten Teilen des Stempels und führt zu Rissen in der Wand an der Unterseite, wo die Kontaktfläche klein ist.
- Risse im Flansch:
- Diese Art der Rissbildung kann auftreten, wenn der Verformungswiderstand der Matrizenschulter die Streckgrenze des Blechzuschnitts überschreitet.
- Risse im Gehäuse:
- Dieser Fehler kann beim Ziehen von Kegeln oder Halbkugeln auftreten, wenn ein Blechzuschnitt mit übermäßig starker Kraft fixiert wird.
- Season Cracking:
- Dies ist eine Art der Rissbildung, die einige Tage nach dem Ziehen auftritt. Das Material härtet nach dem Ziehen aus und die spröder gewordenen Abschnitte reißen aufgrund von Eigenspannungen. Dieser Fehler tritt häufig bei Produkten aus rostfreiem Stahl und Messing auf und kann auch durch feine Risse im Blechzuschnitt verursacht werden.
Falten
Dieser Fehler wird durch die Zug- und Druckkraft verursacht, die während des Ziehens auf den Blechzuschnitt einwirkt.
- Kantenfalte, Wandfalte:
- An Teilen, die durch abgerundete Ecken der Matrize geformt werden, bilden sich Kantenfalten. Falten bilden sich auch an den Wänden unterhalb von Teilen, die durch abgerundete Ecken der Matrize geformt werden. Diese Fehler werden verursacht, wenn das Ziehspiel zu groß ist.
- Gehäusefalte:
- Beim Ziehen von Kegeln oder Halbkugeln können sich Falten auf dem Gehäuse bilden. In einigen Fällen wird dieser Fehler dadurch verursacht, dass der Blechzuschnitt an den abgerundeten Ecken der Matrize und des Stempels nicht wirksam zurückgehalten wird.
- Flanschfalte:
- Diese Fehler treten am Flansch auf. Sie können entstehen, wenn der Blechzuschnitt nicht ausreichend fixiert ist.
Schocklinie
Dies ist ein Fehler, der zu Beginn des Ziehverfahrens auftritt. Er entsteht durch die Spannung, die auf den vom Blechhalter gehaltenen Blechzuschnitt ausgeübt wird, wodurch die Dicke an den abgerundeten Ecken der Matrize verringert wird.
Fresser
Dabei handelt es sich um tiefe Kratzer, die entstehen, wenn der Ölfilm zwischen der Matrize und dem Blechzuschnitt unterbrochen wird, sodass das Blech direkt mit der Matrize oder dem Stempel in Kontakt kommt. Fresser entstehen in Richtung der Stempelbewegung und werden mit fortschreitendem Ziehen größer.
Rückfederung
Rückfederung ist ein Phänomen, bei dem ein gezogenes Werkstück aufgrund von Eigenspannungen im Inneren des geformten Teils leicht in seine ursprüngliche Form zurückkehrt. Rückfederung kann die folgenden Fehler verursachen:
- Winkeländerung:
- Der Winkel des gebogenen Teils ändert sich aufgrund der unterschiedlichen Spannung in Richtung der Blechdicke.
- Wandwölbung:
- Die Wand wölbt sich aufgrund des Spannungsunterschieds in der Längsrichtung.
- Verdrehung:
- Dabei handelt es sich um einen Fehler, bei dem sich das gesamte Teil aufgrund des Spannungsunterschieds in Richtung der Blechdicke und der zur Innenseite der Oberfläche wirkenden Spannung verdreht.
- Verformung der Firstlinie:
- Die Firstlinie wird durch den Spannungsunterschied in Richtung der Blechdicke verformt.
Herausforderungen bei gängigen Dickenmessungen von gezogenen Produkten
Es ist sehr wichtig, sich zu vergewissern, dass die Dicke und die Form eines gezogenen Produkts wie vorgesehen (innerhalb der Toleranzen) sind. Da die Dicke einen großen Einfluss auf die Festigkeit des Produkts hat, sind hochpräzise und quantitative 3D-Formmessungen besonders bei der Messung der Dicke des gesamten Produkts und der Mindestdicke an vertieften Teilen erforderlich.
Normalerweise werden für die Messung 3D-Koordinatenmessgeräte oder Messschieber verwendet, aber diese Methoden sind mit einer Reihe von Herausforderungen verbunden. Dazu gehören die Schwierigkeit, eine genaue Messung mit einem 3D-Koordinatenmessgerät zu erzielen, und die anwenderbedingten Abweichungen bei der Messung mit einem Messschieber.
Herausforderungen bei der Messung – 3D-Koordinatenmessgerät

Bei der Dickenmessung mit einem 3D-Koordinatenmessgerät wird das Messobjekt auf beiden Seiten von einer Messtasterspitze berührt. Wenn die Messfläche groß ist, kann die Genauigkeit erhöht werden, indem die Anzahl der Messpunkte erhöht wird, um mehr Daten zu sammeln.
Die Verwendung eines 3D-Koordinatenmessgeräts für die Dickenmessung von gezogenen Produkten ist jedoch mit den folgenden Schwierigkeiten verbunden:
- Da nur Punktdaten erfasst werden, ist es unmöglich, die wahre Mindestdicke zu überprüfen, selbst wenn Hunderte von Datenpunkten erfasst werden.
- Der Vergleich mit CAD-Daten ist zeit- und arbeitsaufwändig, da die Positionen in den gemessenen Daten nur schwer mit dem CAD-Modell abgeglichen werden können.
- Ein 3D-Koordinatenmessgerät kann bei der Unterscheidung zwischen guten und mangelhaften Werkstücken nur anhand der Messergebnisse (Toleranzwerte) urteilen; es kann sie nicht durch den Vergleich ihrer Formen und das Erkennen der Unterschiede voneinander unterscheiden.
Herausforderungen bei der Messung – Handmessmittel
Handmessmittel wie Messchieber und Mikrometerschrauben sind für Messungen sehr praktisch. Es gibt jedoch zahlreiche Ursachen, die zu Messfehlern oder Abweichungen bei den Messdaten führen.
Bei Handmessmitteln sind die Messbedingungen, wie z. B. die Kontaktkraft (Messkraft) bei der Messung von Hand und die Auswahl der gemessenen Punkte je nach Anwender unterschiedlich. Dies führt zu Schwankungen bei den Messwerten und erschwert quantitative Messungen. Wenn die zu prüfende Fläche groß ist, ist der Zeitaufwand aufgrund der vielen zu messenden Punkte sehr hoch. In manchen Fällen ist die Messung von komplexen Formen und Freiformen unmöglich.
Herausforderungen bei der Dickenmessung
Betrachtet man die Herausforderungen von gängigen Messsystemen stellt sich heraus, dass sie alle die gleichen Herausforderungen haben. Sie erfassen nur Punkt- oder Liniendaten.
Um dies zu umgehen, hat KEYENCE die optischen 3D-Koordinatenmessgeräte der Modellreihe VL entwickelt. Die Modellreihe VL erfasst präzise die 3D-Form der gesamten Oberfläche, ohne das Messobjekt zu berühren. Ein 3D-Scan des Messobjekts auf dem Objekttisch kann in kürzester Zeit abgeschlossen werden, wodurch eine hochpräzise Messung der 3D-Form möglich ist. So lassen sich quantitative Messungen leicht durchführen, ohne dass die Messergebnisse variieren. Einige Vorteile werden nachfolgend erläutert.
Vorteil 1: Einfache Dickenmessung
Die Modellreihe VL kann automatisch die Dicke an bestimmten Punkten berechnen und die Unterschiede farblich darstellen. Wenn Schwellenwerte für die dreifarbige Anzeige festgelegt werden, WITH Durch das Festlegen von Schwellenwerten für die dreifarbige Anzeige, ist es möglich, während der Prüfung eine OK/n.i.O-Beurteilung durchzuführen und die Formen von guten Bauteilen und mangelhaften Bauteilen zu vergleichen. Durch die Verwendung einer Abstufungsanzeige zum Vergleich der gemessenen Daten mit den Entwurfsdaten aus dem Prototyping ist es möglich, Trends in der Dicke zu analysieren, was eine einfache Analyse der Dickenreduzierung und -verteilung ermöglicht.

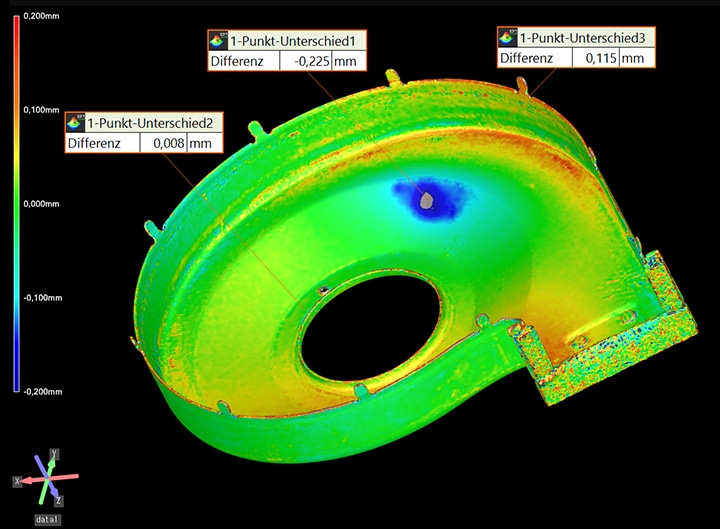
Vorteil 2: Die gesamte 3D-Form wird erfasst.
Wenn ein komplexes Bauteil, das durch Ziehen unregelmäßiger Formen hergestellt wurde und mit einem 3D-Koordinatenmessgerät oder einem Messschieber gemessen wird, erfordert die Messung aufgrund der vielen zu messenden Punkte sehr viel Zeit. Da nur einzelne Punkte gemessen werden, ist es unmöglich, die wahre 3D-Form des Messobjekts zu erfassen.
Mit der Modellreihe VL müssen Sie das Messobjekt nur auf dem Objekttisch platzieren und scannen. Die 3D-Form des Messobjekts kann berührungslos erfasst werden und eine Positionierung ist nicht erforderlich. Da die Profilmessung an jeder beliebigen Stelle des Messobjekts möglich ist, können Sie die Positionen und genauen Zahlenwerte von Formfehlern visualisieren und identifizieren.
Die Modellreihe VL kann Querschnitte von erfassten Daten mit CAD-Daten vergleichen und messen, ohne dass das Werkstück geschnitten werden muss. Die Dickenverhältnisse in den erfassten 3D-Daten können in Farbe visualisiert werden. Dies ermöglicht eine einfache Dickenmessung, ohne das Messobjekt zu berühren. Fehler wie Rückfederung können frühzeitig erkannt werden, indem auf eine falsche Ausrichtung der Schnittprofile geachtet wird. Dadurch können Gegenmaßnahmen wie z. B. eine Druckanpassung durchgeführt werden.


Vorteil 3: Unterschiede zu CAD-Daten können in Farbe visualisiert werden.
Durch den Vergleich der CAD-Daten eines Produkts mit den erfassten Messdaten können Unterschiede zwischen dem tatsächlichen Produkt und den Sollwerten in Farbe visualisiert werden. Dadurch wird der Zeitaufwand für die Analyse der Produktform erheblich reduziert.
Mit der Modellreihe VL lassen sich nicht nur Kantenprofile, sondern auch 2D-, 3D- und Höhenmessungen durchführen.
(Automobilbremsteil)


Zusammenfassung: Effizientere Dickenmessung von gezogenen Produkten
Die Modellreihe VL kann die 3D-Formen von gezogenen Produkten durch 3D-Scans mit hoher Geschwindigkeit genau und sofort messen, ohne das Messobjekt zu berühren, und bietet die folgenden Vorteile:
- Es ist keine Positionierung erforderlich. Legen Sie für die Messung das Messobjekt einfach auf den Objekttisch und starten Sie mittels eines Klicks den Scanvorgang.
- Da die gesamte Oberfläche gemessen wird, ist es möglich, alle Fehlerstellen auf dem Messobjekt zu identifizieren und die Profilmessung an jedem gewünschten Teil durchzuführen.
- Es kann eine Vergleichsmessung zwischen den Scan- und 3D-Daten durchgeführt werden.
- Unterschiede zwischen Scan- und CAD-Daten können farblich dargestellt werden. Die visuell leicht verständlichen Daten ermöglichen es direkt reibungslos Maßnahmen gegen dringende Mängel zu definieren und umzusetzen.
- Die Unterscheidung von i.O./n.i.O.-Produkten und die gemeinsame Nutzung von Daten ermöglicht eine schnelle Analyse von n.i.O-Produkten.
Auf diese Weise kann die Modellreihe VL die Effizienz der Dickenmessung und der Fehleranalyse erheblich verbessern.